ГОСТ Р 50.05.23-2020
НАЦИОНАЛЬНЫЙ СТАНДАРТ РОССИЙСКОЙ ФЕДЕРАЦИИ
Система оценки соответствия в области использования атомной энергии
ОЦЕНКА СООТВЕТСТВИЯ В ФОРМЕ КОНТРОЛЯ
Неразрушающий контроль сварных соединений и наплавленных поверхностей. Нормы оценки качества
Conformity assessment system for the use of nuclear energy. Conformity assessment in the form of examination. Non-destructive examination of welded joints and cladded surfaces. Quality assessment norms
ОКС 25.200
Дата введения 2022-02-01
Предисловие
1 РАЗРАБОТАН Государственной корпорацией по атомной энергии "Росатом"
2 ВНЕСЕН Техническим комитетом по стандартизации ТК 322 "Атомная техника"
3 УТВЕРЖДЕН И ВВЕДЕН В ДЕЙСТВИЕ Приказом Федерального агентства по техническому регулированию и метрологии от 29 декабря 2020 г. N 1433-ст
4 ВВЕДЕН ВПЕРВЫЕ
Правила применения настоящего стандарта установлены в статье 26 Федерального закона от 29 июня 2015 г. N 162-ФЗ "О стандартизации в Российской Федерации". Информация об изменениях к настоящему стандарту публикуется в ежегодном (по состоянию на 1 января текущего года) информационном указателе "Национальные стандарты", а официальный текст изменений и поправок - в ежемесячном информационном указателе "Национальные стандарты". В случае пересмотра (замены) или отмены настоящего стандарта соответствующее уведомление будет опубликовано в ближайшем выпуске ежемесячного информационного указателя "Национальные стандарты". Соответствующая информация, уведомление и тексты размещаются также в информационной системе общего пользования - на официальном сайте Федерального агентства по техническому регулированию и метрологии в сети Интернет ()
Введение
Настоящий стандарт взаимосвязан с другими стандартами, входящими в комплексы стандартов "Система оценки соответствия в области использования атомной энергии. Оценка соответствия в форме контроля" и "Сварка и наплавка оборудования и трубопроводов атомных энергетических установок".
Настоящий стандарт разработан в соответствии с нормативными правовыми актами Российской Федерации в области технического регулирования и использования атомной энергии.
1 Область применения
1.1 Настоящий стандарт устанавливает нормы оценки качества при неразрушающем контроле металла сварных соединений и наплавленных поверхностей при оценке соответствия в форме контроля деталей и сборочных единиц:
а) оборудования и трубопроводов, на которые распространяется действие [1];
б) оборудования и трубопроводов, работающих под избыточным, гидростатическим или вакуумметрическим давлением и отнесенных к элементам третьего класса безопасности, на которые не распространяется действие [1];
в) опор, подвесок, крепежных изделий оборудования и трубопроводов, указанных в перечислениях "а" и "б" настоящего пункта;
г) внутрикорпусных устройств водо-водяных реакторов и реакторов на быстрых нейтронах;
д) металлоконструкций бассейнов выдержки, бассейнов перегрузки и хранения отработавшего ядерного топлива атомных энергетических установок.
1.2 Настоящий стандарт предназначен для оценки соответствия металла сварных соединений и наплавленных поверхностей в форме контроля [2] при изготовлении и монтаже деталей и сборочных единиц оборудования и трубопроводов атомных энергетических установок в соответствии с [3].
1.3 Нормы оценки качества металла сварных соединений и наплавленных поверхностей, изложенные в настоящем стандарте, применяются при контроле с использованием унифицированных методик, входящих в комплекс стандартов "Система оценки соответствия в области использования атомной энергии. Оценка соответствия в форме контроля".
2 Нормативные ссылки
В настоящем стандарте использованы нормативные ссылки на следующие стандарты:
ГОСТ Р 50.05.01 Система оценки соответствия в области использования атомной энергии. Оценка соответствия в форме контроля. Унифицированные методики. Контроль герметичности газовыми и жидкостными методами
ГОСТ Р 50.05.02-2018 Система оценки соответствия в области использования атомной энергии. Оценка соответствия в форме контроля. Унифицированные методики. Ультразвуковой контроль сварных соединений и наплавленных покрытий
ГОСТ Р 50.05.08 Система оценки соответствия в области использования атомной энергии. Оценка соответствия в форме контроля. Унифицированные методики. Визуальный и измерительный контроль
ГОСТ Р 50.05.10 Система оценки соответствия в области использования атомной энергии. Оценка соответствия в форме контроля. Унифицированные методики. Вихретоковый контроль
ГОСТ Р 50.05.25 Система оценки соответствия в области использования атомной энергии. Оценка соответствия в форме контроля. Механические свойства металла сварных соединений и наплавленных поверхностей
ГОСТ Р 59023.2 Сварка и наплавка оборудования и трубопроводов атомных энергетических установок. Основные типы сварных соединений
ГОСТ Р ИСО 6520-1 Сварка и родственные процессы. Классификация дефектов геометрии и сплошности в металлических материалах. Часть 1. Сварка плавлением
Примечание - При пользовании настоящим стандартом целесообразно проверить действие ссылочных стандартов в информационной системе общего пользования - на официальном сайте Федерального агентства по техническому регулированию и метрологии в сети Интернет или по ежегодному информационному указателю "Национальные стандарты", который опубликован по состоянию на 1 января текущего года, и по выпускам ежемесячного информационного указателя "Национальные стандарты" за текущий год. Если заменен ссылочный стандарт, на который дана недатированная ссылка, то рекомендуется использовать действующую версию этого стандарта с учетом всех внесенных в данную версию изменений. Если заменен ссылочный стандарт, на который дана датированная ссылка, то рекомендуется использовать версию этого стандарта с указанным выше годом утверждения (принятия). Если после утверждения настоящего стандарта в ссылочный стандарт, на который дана датированная ссылка, внесено изменение, затрагивающее положение, на которое дана ссылка, то это положение рекомендуется применять без учета данного изменения. Если ссылочный стандарт отменен без замены, то положение, в котором дана ссылка на него, рекомендуется применять в части, не затрагивающей эту ссылку.
3 Термины и определения
В настоящем стандарте применены термины по ГОСТ Р ИСО 6520-1 и ГОСТ Р 50.05.08, а также следующие термины с соответствующими определениями:
3.1 бугристость: Высота выпуклости сварного шва над поверхностью основного металла.
3.2 включение: Твердая частица инородного вещества в основном или наплавленном металле или металле шва или полость, заполненная газом, шлаком.
Примечание - Одиночная несплошность определяется аналогичным образом.
3.4 включение одиночное мелкое (при радиографическом контроле): Включение, допустимость которого устанавливается в зависимости от его размера, а также от общего количества и суммарной приведенной площади таких включений и одиночных скоплений.
3.5 включение одиночное крупное (при радиографическом контроле): Включение, максимальный размер которого превышает допустимый размер одиночных мелких включений, а допустимость устанавливается только в зависимости от размеров и количества без учета их площади при подсчете суммарной приведенной площади и без включения их в общее количество одиночных мелких включений и одиночных скоплений.
3.6 внешний контур скопления: Контур, ограниченный внешними краями включений, входящих в скопление, и касательными линиями, соединяющими указанные края (рисунок 2).
Рисунок 1 - Условия одиночности двух рассматриваемых включений
![]() |
1 - внешний контур скопления
3.7 вогнутость корня шва: Углубление на поверхности сварного соединения с односторонним швом в месте расположения его корня (оценивается по максимальной глубине расположения поверхности корня шва от уровня расположения поверхностей сваренных деталей).
3.8 вогнутость углового шва: Максимальное расстояние от поверхности шва до линии, соединяющей края его поверхности в одном поперечном сечении (оценивается по максимальной глубине расположения поверхности шва под указанной линией).
3.9 выпуклость корня шва: Часть одностороннего сварного шва со стороны его корня, выступающая над уровнем расположения поверхностей сваренных деталей (оценивается по максимальной высоте расположения поверхности корня шва над указанным уровнем).
3.10 выпуклость стыкового шва: Часть стыкового сварного шва, выступающая над уровнем расположения поверхностей сваренных деталей (оценивается по максимальной высоте расположения поверхности шва над указанной линией).
3.11 выпуклость углового шва: Часть углового сварного шва, выступающая над линией, соединяющей края его поверхности в одном поперечном сечении (оценивается по максимальной высоте расположения поверхности над указанной линией).
3.12 группа включений: Два или несколько включений, минимальное расстояние между краями которых менее максимальной ширины хотя бы одного из двух рассматриваемых соседних включений; внешний контур рассматриваемой группы включений ограничивается внешними краями включений, входящих в рассматриваемую группу, и касательными линиями, соединяющими указанные края (рисунок 3).
![]() |
Рисунок 3 - Группа включений
3.13 западание между валиками: Продольная впадина между двумя соседними валиками (слоями) шва (оценивается по максимальной глубине).
3.14 индикаторный след (индикаторный рисунок) при капиллярном контроле: След, образованный индикаторным пенетрантом на слое проявителя над несплошностью.
3.15 индикаторный след (индикаторный рисунок) при контроле магнитопорошковым методом: Видимая длина валика осаждения магнитного порошка над несплошностью.
3.16 линейный индикаторный след: Индикаторный след, обнаруженный в процессе неразрушающего контроля, у которого длина больше ширины более чем в три раза.
![]() |
3.18 максимальный размер скопления A: расстояние между двумя наиболее удаленными друг от друга точками внешнего контура скопления (рисунок 2).
3.20 максимальная ширина скопления B: Наибольшее расстояние между двумя точками внешнего контура скопления, измеренное в направлении, перпендикулярном максимальному размеру скопления (рисунок 2).
3.21
непровар: Несплавление в сварном соединении или наплавленной детали между основным металлом и металлом шва (наплавленным металлом) или между отдельными валиками. [[3], приложение 1] |
3.22 недопустимые включения и скопления: Одиночные включения и скопления, превышающие установленные нормы по размерам, количеству или суммарной приведенной площади, а также все неодиночные включения и скопления, т.е. включения и скопления, расстояния между которыми меньше указанных в 3.3 и 3.34.
3.23
несплошность: Нарушение однородности металла, вызывающее скачкообразное изменение одной или нескольких физических характеристик, определяемых методами неразрушающего контроля. Примечание - Несплошность - обобщенное наименование трещин, отслоений, прожогов, свищей, пор, непроваров и включений. [[3], приложение 1] |
3.24
номинальная толщина основного металла наплавленной детали: Указанная в конструкторской документации (без учета допусков) толщина основного металла детали. [[3], приложение 1] |
3.25
номинальная толщина сваренных деталей: Указанная в конструкторской документации (без учета допусков) толщина основного металла деталей в зоне, примыкающей к сварному шву. [[3], приложение 1] |
3.26 норма оценки качества сварного соединения (наплавленной поверхности): Наибольшее или наименьшее регламентированное значение показателя качества сварного соединения (наплавленной поверхности), а именно количество и размеры несплошностей, геометрические характеристики сварного соединения: чешуйчатость, западания между валиками, вогнутость и выпуклость корня шва.
3.27
округлый индикаторный след: Индикаторный след с отношением его максимального размера к максимальной ширине, равным трем или менее. [ГОСТ Р 50.05.09-2018, пункт 3.12] |
3.28 поднаплавочная трещина: Трещина в основном металле или перлитной части сварного соединения, выходящая на границу раздела с антикоррозионной наплавкой.
3.29 приведенная площадь включения или скопления (при радиографическом контроле): Произведение максимального размера включения (скопления) на его максимальную ширину (учитывается для одиночных малых включений и одиночных скоплений).
3.30 протяженная несплошность (кроме ультразвукового контроля): Несплошность с отношением максимальной длины к максимальной ширине более трех (ширина измеряется в направлении, перпендикулярном к линии максимальной длины).
3.32
свищ: Дефект в виде воронкообразного или трубчатого углубления в сварном шве. [[3], приложение 1] |
3.33 скопление: Два или несколько включений (пор, шлаковых и вольфрамовых включений) с наибольшим размером более 0,2 мм (рисунок 6), минимальное расстояние между краями которых меньше установленного для одиночных включений, но не менее максимальной ширины каждого из двух рассматриваемых любых соседних включений.
Примечание - При оценке расстояний между скоплениями и включениями скопление рассматривается как одиночное включение.
![]() |
Рисунок 5 - Расчетная высота углового шва
![]() |
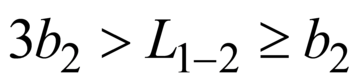
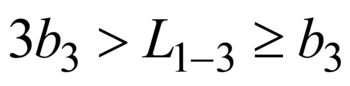
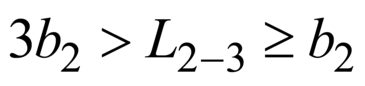
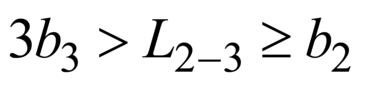
Рисунок 6 - Скопление
![]() |
Рисунок 7 - Одиночные скопления
3.35
трещина: Дефект в виде разрыва металла сварного соединения или наплавленной детали (изделия). [[3], приложение 1] |
3.36
условный размер (протяженность, ширина, высота) дефекта (при ультразвуковом контроле): Размер в миллиметрах, соответствующий зоне между крайними положениями преобразователя, в пределах которой фиксируют сигнал от несплошности при заданном уровне чувствительности. [ГОСТ Р 50.05.02-2018, пункт 3.4] |
3.37
суммарная приведенная площадь скоплений или включений (при радиографическом контроле): Сумма приведенных площадей отдельных одиночных мелких включений и одиночных скоплений. [[3], приложение 1] |
3.38 эквивалентная площадь несплошности (при ультразвуковом контроле): Площадь плоскодонного искусственного отражателя, ориентированного перпендикулярно акустической оси преобразователя и расположенного на том же расстоянии от пьезоэлектрического преобразователя, что и реальная несплошность, при которой значения сигнала акустического прибора от несплошности равны.
4 Обозначения
В настоящем стандарте применены следующие обозначения:
5 Оценка качества сварных соединений и наплавленных поверхностей
5.1 Общие требования
5.1.1 Нормы оценки качества сварных соединений устанавливают в зависимости от категории сварного соединения по классификации, приведенной в федеральных нормах и правилах в области использования атомной энергии [2].
5.1.2 Нормы оценки качества уплотнительных и антикоррозионных наплавленных поверхностей установлены для всех категорий сварных соединений по классификации, приведенной в федеральных нормах и правилах в области использования атомной энергии [2].
5.1.3 Нормы допустимых размеров несплошностей в сварных соединениях следует принимать:
а) для стыковых сварных соединений различной толщины - по номинальной толщине более тонкой детали;
б) для угловых и тавровых сварных соединений - по расчетной высоте углового шва;
в) для торцевых сварных соединений - по удвоенной номинальной толщине более тонкой свариваемой детали. В случае деталей одинаковой толщины - по удвоенной номинальной толщине.
Примечание - Для нахлесточных соединений нормы оценки качества устанавливает проектная (конструкторская) организация;
г) для сварных соединений труб с трубными досками - по номинальной толщине стенки труб;
д) для стыковых сварных соединений, выполненных с расточкой, - по номинальной толщине стенки в месте расточки;
е) при радиографическом контроле сварных соединений труб или других цилиндрических деталей через две стенки - по номинальной толщине одной стенки.
Протяженность (длину) сварных соединений определяют по их наружной поверхности (для кольцевых, угловых и тавровых сварных соединений - по наружной поверхности привариваемой детали у края углового шва).
5.1.4 Геометрические параметры выполненных швов (ширина и высота выпуклости шва, минимальное расстояние от края выпуклости шва до линии сплавления предварительной наплавки с основным металлом) должны соответствовать требованиям ГОСТ Р 59023.2 и/или конструкторской документации.
5.1.5 Выявленные при визуальном и измерительном контроле несплошности, размеры которых превышают допустимые, должны быть устранены по технологической документации организации-изготовителя до проведения контроля другими методами.
5.1.6 Трещины, отслоения, прожоги, свищи, наплывы, усадочные раковины, подрезы, брызги металла, непровары, скопления и неодиночные включения, выявленные при визуальном и измерительном контроле, не допускаются.
5.1.7 При невозможности контроля выпуклости и вогнутости корней сварных швов визуальным и измерительным контролем данные параметры определяют при радиографическом контроле (см. таблицы 3, 4, 5, 6, 7).
5.1.8 На сварных соединениях титановых сплавов величина твердости по Виккерсу в металле шва не должна превышать 230 единиц при сварке проволокой ВТ1-00св, 300 единиц - ПТ-7Мсв, 350 единиц - ВТ6св. Твердость в зоне температурного влияния не должна превышать твердости основного металла. Допускаются единичные выпады до 400 единиц, если замеры твердости вокруг этой точки не превышают приведенных выше значений.
5.2 Оценка качества при визуальном и измерительном контроле
5.2.1 Сталь и железоникелевые сплавы
5.2.1.1 Нормы допустимых одиночных поверхностных включений для сварных соединений и предварительно наплавленных кромок деталей и сборочных единиц из стали и железоникелевых сплавов приведены в таблице 1.
Таблица 1
Номинальная толщина сваренных деталей, мм | Допустимый максимальный размер включения в сварных соединениях (предварительно наплавленных кромках) категорий, мм | Максимально допустимое количество включений на любом участке длиной 100,0 мм сварного соединения (предварительно наплавленной кромки) категорий | ||||||||
| Iн | IIн | I | II | III | Iн | IIн | I | II | III |
До 2,0 включ. | - | - | - | - | 0,3 | - | - | - | - | 2 |
Св. 2,0 до 3,0 включ. | - | - | - | 0,3 | 0,4 | - | - | - | 2 | 3 |
Св. 3,0 до 4,0 включ. | - | - | 0,3 | 0,4 | 0,5 | - | - | 2 | 3 | 4 |
Св. 4,0 до 5,0 включ. | - | 0,3 | 0,4 | 0,5 | 0,6 | - | 2 | 2 | 3 | 4 |
Св. 5,0 до 6,0 включ. | 0,3 | 0,4 | 0,5 | 0,6 | 0,8 | 2 | 2 | 2 | 3 | 4 |
Св. 6,0 до 8,0 включ. | 0,4 | 0,5 | 0,6 | 0,8 | 1,0 | 2 | 2 | 3 | 4 | 5 |
Св. 8,0 до 10,0 включ. | 0,5 | 0,6 | 0,8 | 1,0 | 1,2 | 2 | 3 | 3 | 4 | 5 |
Св. 10,0 до 15,0 включ. | 0,6 | 0,8 | 1,0 | 1,2 | 1,5 | 3 | 3 | 3 | 4 | 5 |
Св. 15,0 до 20,0 включ. | 0,8 | 1,0 | 1,2 | 1,5 | 2,0 | 3 | 3 | 4 | 5 | 6 |
Св. 20,0 до 40,0 включ. | 1,0 | 1,2 | 1,5 | 2,0 | 2,0 | 3 | 4 | 4 | 5 | 6 |
Св. 40,0 до 100,0 включ. | 1,2 | 1,5 | 1,5 | 2,0 | 2,5 | 4 | 4 | 5 | 6 | 7 |
Св. 100,0 до 200,0 включ. | 1,5 | 1,5 | 1,5 | 2,0 | 2,5 | 4 | 5 | 6 | 7 | 8 |
Св. 200,0 | 1,5 | 1,5 | 1,5 | 2,0 | 2,5 | 5 | 6 | 7 | 8 | 9 |
Примечания 1 Включения с наибольшим фактическим размером до 0,2 мм не учитываются. 2 Прочерк означает, что включения допустимы с учетом примечания 1 (включения размером от 0,2 мм до допустимого максимального размера допускаются и фиксируются при контроле). |
5.2.1.2 Максимальная допустимая высота (глубина) западания между валиками для сварных соединений деталей и сборочных единиц из стали и железоникелевых сплавов приведена в таблице 2.
Таблица 2
Номинальная толщина сваренных деталей, мм | Максимальная высота (глубина) западания, мм, для категорий сварных соединений | ||
| I, Iн, IIн | II | III |
До 2,0 включ. | 0,3 | 0,4 | 0,6 |
Св. 2,0 до 4,0 включ. | 0,4 | 0,6 | 0,8 |
Св. 4,0 до 6,0 включ. | 0,6 | 0,8 | 1,0 |
Св. 6,0 до 10,0 включ. | 0,8 | 1,0 | 1,2 |
Св. 10,0 до 15,0 включ. | 1,0 | 1,2 | 1,5 |
Св. 15,0 | 1,2 | 1,5 | 2,0 |
5.2.1.3 При сварке поворотных стыков трубных деталей из стали без подкладных колец допускается вогнутость корня шва с внутренней стороны, размеры которой не превышают значений, приведенных в таблице 3.
Таблица 3
Номинальная толщина стенки сваренных труб (деталей), мм | Допустимая высота (глубина) вогнутости корня шва, мм |
От 1,0 до 1,8 включ. | 0,2 |
Св. 1,8 до 2,8 включ. | 0,4 |
Св. 2,8 до 4,0 включ. | 0,6 |
Св. 4,0 до 6,0 включ. | 0,8 |
Св. 6,0 до 8,0 включ. | 1,0 |
Св. 8,0 до 12,0 включ. | 1,2 |
Св. 12,0 | 1,5 |
5.2.1.4 При сварке неповоротных стыков труб из стали без подкладных колец допускается вогнутость корня шва с внутренней стороны, размеры которой не превышают значений, приведенных в таблице 4.
Таблица 4
Номинальная толщина стенки сваренных труб (деталей), , мм | Допустимая высота (глубина) вогнутости корня шва, мм |
От 1,0 до 1,8 включ. | 0,4 |
Св. 1,8 до 2,8 включ. | 0,6 |
Св. 2,8 до 4,0 включ. | 0,8 |
Св. 4,0 до 6, 0 включ. | 1,0 |
Св. 6,0 до 8,0 включ. | 1,2 |
Св. 8,0 | 0,15 , но не более 1,6 мм при условии увеличения выпуклости шва на 1,0 мм от номинального размера |
5.2.1.5 Размеры сплошной или прерывистой выпуклости корня шва при односторонней сварке стальных труб без подкладных колец должны соответствовать нормам, приведенным в таблице 5.
Таблица 5
Номинальный внутренний диаметр трубы, мм | Размер выпуклости, мм, не более |
До 25,0 включ. | 1,5 |
Св. 25,0 до 150,0 включ. | 2,0 |
Св. 150,0 | 2,5 |
5.2.2 Алюминиевые сплавы
5.2.2.1 Нормы допустимых одиночных поверхностных включений и отклонений от геометрических размеров сварных соединений деталей и сборочных единиц из алюминиевых сплавов приведены в таблице 6.
Таблица 6
Наименование контролируемого параметра | Кате- гория сварного соеди- нения | Номинальная толщина и диаметр сваренных деталей, мм | Допустимый наибольший размер несплошности, мм | Допустимое количество несплошностей или их суммарная протяженность |
Глубина подреза основного металла | I, II, III | Все толщины | 0,1 , но не более 0,5 | 10% длины контролируемого сварного шва с длиной отдельных участков не более 50,0 мм на любых 100,0 мм контролируемого участка |
Западания между валиками, бугристость и чешуйчатость | I | Все толщины | 0,1 , но не более 0,8 | Не регламентируется |
II, III | до 10,0 включ. | Не более 1,0 |
| |
II, III | Св. 10,0 до 20,0 включ. | Не более 1,2 |
| |
| Св. 20,0 | Не более 1,5 |
| |
Включения вольфрамовые | I | Все толщины | 0,1 , но не более 2,0 | 1 на каждые 100,0 мм шва |
II, III |
| 0,1 | 3 на каждые 100,0 мм шва | |
Вогнутость корня шва при сварке поворотных стыков труб без подкладных колец | I, II, III | Св. 1,0 до 2,0 включ. | Не более 0,2 | Не регламентируется |
| Св. 2,0 до 3,0 включ. | Не более 0,4 |
| |
| Св. 3,0 до 4,0 включ. | Не более 0,6 |
| |
| Св. 4,0 до 6,0 включ. | Не более 0,8 |
| |
| Св. 6,0 до 8,0 включ. | Не более 1,0 |
| |
| Св. 8,0 до 12,0 включ. | Не более 1,2 |
| |
| Св. 12,0 | Не более 1,5 |
| |
Вогнутость корня шва при сварке неповоротных стыков труб без подкладных колец | I, II, III | Св. 1,0 до 2,0 включ. | Не более 0,4 | Не регламентируется |
|
| Св. 2,0 до 3,0 включ. | Не более 0,6 |
|
|
| Св. 3,0 до 4,0 включ. | Не более 0,8 |
|
|
| Св. 4,0 до 6,0 включ. | Не более 1,0 |
|
|
| Св. 6,0 до 8,0 включ. | Не более 1,2 |
|
| Св. 8,0 | 0,15 , но не более 1,6 мм при условии увеличения усиления шва на 1,0 мм от номинального |
| |
Выпуклость корня шва при односторонней сварке труб без подкладных колец | I, II, III | до 25,0 включ. | Не более 1,5 | Не регламентируется |
| св. 25,0 до 150,0 включ. | Не более 2,0 | ||
| св. 150,0 | Не более 2,5 | ||
Примечание - - минимальная номинальная толщина сварных деталей. |
5.2.3 Титановые сплавы
5.2.3.1 Нормы оценки качества сварных соединений I-III категорий деталей и сборочных единиц из титановых сплавов по результатам визуального и измерительного контроля приведены в таблице 7.
Таблица 7
Сварное соединение | Нормы оценки качества, мм | ||||||
Номинальная толщина сваренных деталей, мм | Кате- гория свар- ного соеди- нения | Радиус перехода , мм, не менее | Подрезы зоны сплавления | Западания между валиками и чешуйчатость, не более | Размеры формирования корня шва, не более | ||
|
|
| глубина, не более | ширина |
| вогнутость | превышение выпуклости |
До 5,0 включ. | I, II | 12 | 0,5 | 1,0 | 0,5 | 0,5 | 1,0 |
III | 6 | 1,0 | 1,5 | 0,5 q 1,0 | 1,0 | 1,5 | |
Св. 5,0 до 12,0 включ. | I, II | 12 | 0,5 | 1,0 | 0,5 q 1,0 | 1,0 | 1,5 |
III | 6 | 1,0 | 1,5 | 0,5 q 1,0 | 1,5 | 2,0 | |
Св. 12,0 | I, II | 12 | 0,5 | 1,0 | 0,5 q 1,5 | 1,5 | 2,0 |
| III | 6 | 1,0 | 1,5 | 0,5 q 2,0 | 2,0 | 3,0 |
5.2.3.2 На сварных соединениях титановых сплавов не допускаются соломенные, коричневые или синие цвета побежалости.
5.3 Оценка качества при прогонке металлическим калибром (шариком)
5.3.1 Результаты контроля прогонкой металлическим калибром (шариком) считаются удовлетворительными, если калибр (шарик) заданного конструкторской документацией диаметра проходит через трубу с контролируемым сварным соединением.
5.4 Оценка качества при контроле герметичности
5.4.1 Качество сварного соединения считается удовлетворительным, если в результате контроля герметичности установлено, что измеренные характеристики герметичности сварного соединения соответствуют требованиям, установленным конструкторской документацией.
Примечания
1 Конструкторской документацией могут быть установлены требования в виде норм или классов герметичности в соответствии с требованиями ГОСТ Р 50.05.01.
2 Конкретный метод и способ контроля герметичности, назначенный организацией-изготовителем (монтажной организацией) в соответствии с требованиями герметичности сварного соединения, обеспечивает определение фактических показателей герметичности.
5.5 Оценка качества при капиллярном контроле
5.5.1 Оценку качества сварных соединений и наплавленных поверхностей при капиллярном контроле допускается проводить по индикаторным следам и по измеренным значениям характеристик выявленных несплошностей после удаления проявителя в зоне зафиксированных индикаторных следов.
5.5.2 При капиллярном контроле по индикаторным следам качество сварного соединения или наплавленной поверхности считается удовлетворительным при одновременном соблюдении следующих условий:
а) индикаторные следы являются одиночными;
б) линейные индикаторные следы отсутствуют;
в) наибольший размер каждого индикаторного следа не превышает более чем в три раза значений, приведенных в 5.2.1.1 и 6.1.1 для одиночных включений;
г) количество индикаторных следов не превышает значений, приведенных в 5.2.1.1 и 6.1.1 для одиночных включений.
5.5.3 Индикаторные следы считаются одиночными, если минимальное расстояние от края каждого из них до края другого соседнего индикаторного следа не менее максимального размера индикаторного следа с меньшим значением этого показателя.
5.5.4 Округлые индикаторные следы с наибольшим размером до 0,6 мм включительно не учитывают вне зависимости от номинальной толщины сваренных (наплавленных) деталей.
5.5.5 Несплошности, не соответствующие требованиям 5.5.4, допускается подвергать контролю по фактическим размерам, результаты которого являются окончательными.
5.5.6 Оценку качества сварного соединения и наплавленной поверхности при проведении капиллярного контроля по фактическим характеристикам выявленных несплошностей следует проводить в соответствии с нормами оценки качества, указанными в 5.2.1.1, 5.2.1.2 и 6.1.2.
5.6 Оценка качества при магнитопорошковом контроле
5.6.1 Оценку качества при магнитопорошковом контроле следует проводить в соответствии с требованиями, установленными для визуального контроля в 5.2.1.1, 5.2.1.2. Допускается оценивать выявленные несплошности, выходящие на поверхность, по их фактическим характеристикам после удаления суспензии или порошка.
5.6.2 При выявлении индикаторных рисунков недопустимых размеров допускается проведение капиллярного контроля зон, где данные индикаторные рисунки были выявлены.
5.6.3 При отсутствии дефектов по результатам капиллярного контроля проводят зашлифовку металла на глубину до 1,0 мм (при условии обеспечения минимально допустимой толщины металла) и последующий повторный магнитопорошковый контроль, результаты которого являются окончательными.
5.7 Оценка качества при радиографическом контроле
5.7.1 Общие требования
5.7.1.1 Качество сварного соединения (или наплавленной поверхности) деталей и сборочных единиц считается удовлетворительным, если при контроле не обнаружены трещины, непровары, подрезы, а также не соответствующие требованиям настоящего стандарта включения, вогнутость или выпуклость корня шва. Нормы на высоту (глубину) вогнутости или выпуклости корня шва принимают в соответствии с 5.2.1.3-5.2.1.5, а также 5.2.2.1 и 5.2.3.1.
5.7.1.2 Если вогнутость или превышение выпуклости корня шва проверены при измерительном контроле, их проверку при радиографическом контроле не проводят.
5.7.1.3 При определении скопления учитывают любые включения, наибольший размер которых превышает 0,2 мм.
5.7.1.4 Любую совокупность включений (одиночных скоплений, групп включений), которая может быть вписана в прямоугольник с размерами сторон, не превышающими значений допускаемого максимального размера и допускаемой максимальной ширины одиночного крупного включения, необходимо рассматривать как одно включение.
5.7.1.5 Любую совокупность включений (одиночных скоплений, групп включений), которая может быть вписана в квадрат с размером стороны, не превышающим значения допускаемого максимального размера одиночного включения, необходимо рассматривать как одно включение.
5.7.1.6 При контроле сварных соединений с неполным проплавлением или с подкладными кольцами, или на "усе" видимые на радиографическом снимке конструкционные зазоры, в том числе заполненные затекшим шлаком или металлом, не являются браковочным признаком и должны быть отражены в примечании заключения радиографического контроля.
Примечание - "Ус" - это технологическая часть кромки в виде подкладки, выступающая изнутри одной из свариваемых деталей.
5.7.2 Сталь и железоникелевые сплавы
5.7.2.1 Нормы допустимых одиночных включений и скоплений для сварных соединений (кроме Iн и IIн категорий) деталей и сборочных единиц из стали и железоникелевых сплавов приведены в таблице 8.
Таблица 8
Номинальная толщина сваренных деталей, мм | Требуемая чувстви- тельность контроля, мм, не более | Одиночные включения и скопления | Одиночные крупные включения | |||||
|
| Допустимый наибольший размер, мм | Допус- тимое коли- чество вклю- чений и скоп- лений на любом участке сварного соеди- нения длиной 100,0 мм, шт. | Допустимая суммарная приве- денная площадь включений и скоплений на любом участке сварного соеди- нения длиной 100,0 мм, мм | Допустимые размеры, мм | Допус- тимое коли- чество на любом участке свар- ного соеди- нения длиной 100,0 мм, шт. | ||
|
| вклю- чения | скоп- ления |
|
| наиболь- ший размер | наиболь- шая ширина |
|
Сварные соединения I категории | ||||||||
Св. 1,0 до 1,5 включ. | 0,10 | 0,2 | 0,3 | 10 | 0,15 | 3,0 | 0,2 | 1 |
Св. 1,5 до 2,0 включ. | 0,10 | 0,3 | 0,4 | 10 | 0,3 | 3,0 | 0,3 | 1 |
Св. 2,0 до 2,5 включ. | 0,10 | 0,4 | 0,6 | 10 | 0,6 | 3,0 | 0,4 | 1 |
Св. 2,5 до 3,0 включ. | 0,10 | 0,5 | 0,8 | 10 | 1,0 | 3,0 | 0,5 | 1 |
Св. 3,0, до 4,5 включ. | 0,10 | 0,6 | 1,0 | 10 | 1,4 | 3,0 | 0,6 | 1 |
Св. 4,5 до 6,0 включ. | 0,20 | 0,8 | 1,2 | 11 | 2,5 | 3,0 | 0,8 | 1 |
Св. 6,0 до 7,5 включ. | 0,20 | 1,0 | 1,5 | 11 | 4,0 | 3,0 | 1,0 | 1 |
Св. 7,5 до 10,0 включ. | 0,20 | 1,2 | 2,0 | 12 | 5,5 | 3,5 | 1,2 | 1 |
Св. 10,0 до 12,0 включ. | 0,20 | 1,5 | 2,5 | 12 | 7,5 | 3,5 | 1,5 | 1 |
Св. 12,0 до 14,0 включ. | 0,30 | 1,5 | 2,5 | 13 | 9,0 | 4,0 | 1,5 | 1 |
Св. 14,0 до 18,0 включ. | 0,30 | 2,0 | 3,0 | 13 | 11,0 | 4,0 | 2,0 | 1 |
Св. 18,0 до 21,0 включ. | 0,30 | 2,0 | 3,0 | 14 | 14,0 | 4,0 | 2,0 | 1 |
Св. 21,0 до 24,0 включ. | 0,40 | 2,0 | 3,0 | 14 | 17,5 | 5,0 | 2,0 | 1 |
Св. 24,0 до 27,0 включ. | 0,40 | 2,5 | 3,5 | 15 | 20,0 | 5,0 | 2,5 | 2 |
Св. 27,0 до 30,0 включ. | 0,40 | 2,5 | 3,5 | 15 | 23,0 | 6,0 | 2,5 | 2 |
Св. 30,0 до 35,0 включ. | 0,50 | 2,5 | 4,0 | 16 | 26,0 | 6,0 | 2,5 | 2 |
Св. 35,0 до 40,0 включ. | 0,50 | 3,0 | 4,5 | 17 | 30,0 | 7,0 | 3,0 | 2 |
Св. 40,0 до 45,0 включ. | 0,60 | 3,0 | 4,5 | 18 | 34,0 | 8,0 | 3,0 | 2 |
Св. 45,0 до 50,0 включ. | 0,60 | 3,0 | 4,5 | 19 | 38,0 | 9,0 | 3,0 | 2 |
Св. 50,0 до 55,0 включ. | 0,60 | 3,0 | 4,5 | 20 | 42,0 | 10,0 | 3,0 | 2 |
Св. 55,0 до 65,0 включ. | 0,75 | 3,5 | 5,0 | 21 | 48,0 | 10,0 | 3,5 | 2 |
Св. 65,0 до 75,0 включ. | 0,75 | 3,5 | 5,0 | 22 | 56,0 | 10,0 | 3,5 | 2 |
Св. 75,0 до 85,0 включ. | 1,00 | 4,0 | 6,0 | 23 | 64,0 | 10,0 | 4,0 | 2 |
Св. 85,0 до 100,0 включ. | 1,00 | 4,0 | 6,0 | 24 | 72,0 | 10,0 | 4,0 | 2 |
Св. 100,0 до 115,0 включ. | 1,25 | 4,0 | 6,0 | 25 | 85,0 | 10,0 | 4,0 | 2 |
Св. 115,0 до 125,0 включ. | 1,25 | 5,0 | 7,0 | 25 | 100,0 | 10,0 | 5,0 | 2 |
Св. 125,0 до 135,0 включ. | 1,50 | 5,0 | 7,0 | 24 | 100,0 | 11,0 | 5,0 | 2 |
Св. 135,0 до 150,0 включ. | 1,50 | 5,0 | 7,0 | 24 | 115,0 | 11,0 | 5,0 | 2 |
Св. 150,0 до 175,0 включ. | 2,00 | 5,0 | 7,0 | 23 | 130,0 | 11,0 | 5,0 | 2 |
Св. 175,0 до 200,0 включ. | 2,00 | 5,0 | 8,0 | 23 | 150,0 | 11,0 | 5,0 | 2 |
Св. 200,0 до 250,0 включ. | 2,50 | 5,0 | 8,0 | 22 | 180,0 | 12,0 | 5,0 | 2 |
Св. 250,0 до 300,0 включ. | 3,00 | 6,0 | 9,0 | 21 | 220,0 | 12,0 | 6,0 | 2 |
Св. 300,0 до 350,0 включ. | 3,50 | 7,0 | 10,0 | 20 | 260,0 | 13,0 | 7,0 | 2 |
Св. 350,0 до 400,0 включ. | 4,00 | 8,0 | 12,0 | 19 | 300,0 | 13,0 | 8,0 | 2 |
Св. 400,0 до 450,0 включ. | 4,50 | 9,0 | 14,0 | 18 | 340,0 | 13,0 | 9,0 | 2 |
Св. 450,0 до 500,0 включ. | 5,00 | 10,0 | 15,0 | 17 | 380,0 | 14,0 | 10,0 | 2 |
Св. 500,0 до 550,0 включ. | 5,50 | 11,0 | 16,0 | 16 | 420,0 | 14,0 | 11,0 | 2 |
Св. 550,0 | 6,00 | 12,0 | 18,0 | 15 | 460,0 | 14,0 | 12,0 | 2 |
Сварные соединения II категории | ||||||||
Св. 1,0 до 1,5 включ. | 0,10 | 0,3 | 0,4 | 11 | 0,4 | 4,0 | 0,3 | 1 |
Св. 1,5 до 2,0 включ. | 0,10 | 0,4 | 0,6 | 11 | 0,6 | 4,0 | 0,4 | 1 |
Св. 2,0 до 2,5 включ. | 0,10 | 0,5 | 0,8 | 11 | 1,2 | 4,0 | 0,5 | 1 |
Св. 2,5 до 3,5 включ. | 0,10 | 0,6 | 1,0 | 11 | 1,7 | 4,0 | 0,6 | 1 |
Св. 3,5 до 5,0 включ. | 0,20 | 0,8 | 1,2 | 11 | 3,0 | 4,0 | 0,8 | 1 |
Св. 5,0 до 6,5 включ. | 0,20 | 1,0 | 1,5 | 12 | 4,5 | 4,0 | 1,0 | 2 |
Св. 6,5 до 8,5 включ. | 0,20 | 1,2 | 2,0 | 12 | 6,5 | 4,0 | 1,2 | 2 |
Св. 8,5 до 10,0 включ. | 0,20 | 1,5 | 2,5 | 13 | 8,5 | 4,0 | 1,5 | 2 |
Св. 10,0 до 12,0 включ. | 0,30 | 1,5 | 2,5 | 13 | 10,0 | 5,0 | 1,5 | 2 |
Св. 12,0 до 15,0 включ. | 0,30 | 2,0 | 3,0 | 14 | 12,0 | 5,0 | 2,0 | 2 |
Св. 15,0 до 18,0 включ. | 0,30 | 2,0 | 3,0 | 14 | 15,0 | 5,0 | 2,0 | 2 |
Св. 18,0 до 21,0 включ. | 0,40 | 2,5 | 3,5 | 15 | 18,0 | 6,0 | 2,5 | 2 |
Св. 21,0 до 24,0 включ. | 0,40 | 2,5 | 4,0 | 15 | 21,0 | 6,0 | 2,5 | 2 |
Св. 24,0 до 28,0 включ. | 0,50 | 3,0 | 4,5 | 16 | 24,0 | 7,0 | 3,0 | 2 |
Св. 28,0 до 32,0 включ. | 0,50 | 3,0 | 4,5 | 16 | 28,0 | 7,0 | 3,0 | 2 |
Св. 32,0 до 38,0 включ. | 0,60 | 3,0 | 4,5 | 18 | 32,0 | 8,0 | 3,0 | 2 |
Св. 38,0 до 44,0 включ. | 0,60 | 3,5 | 5,0 | 20 | 37,0 | 9,0 | 3,5 | 2 |
Св. 44,0 до 52,0 включ. | 0,75 | 3,5 | 5,0 | 21 | 43,0 | 10,0 | 3,5 | 2 |
Св. 52,0 до 60,0 включ. | 0,75 | 4,0 | 6,0 | 22 | 50,0 | 12,0 | 4,0 | 3 |
Св. 60,0 до 70,0 включ. | 1,00 | 4,0 | 6,0 | 23 | 58,0 | 12,0 | 4,0 | 3 |
Св. 70,0 до 80,0 включ. | 1,00 | 4,0 | 6,0 | 24 | 67,0 | 12,0 | 4,0 | 3 |
Св. 80,0 до 100,0 включ. | 1,25 | 4,0 | 6,0 | 25 | 81,0 | 12,0 | 4,0 | 3 |
Св. 100,0 до 120,0 включ. | 1,50 | 5,0 | 7,0 | 26 | 100,0 | 12,0 | 5,0 | 3 |
Св. 120,0 до 140,0 включ. | 1,75 | 5,0 | 7,0 | 25 | 115,0 | 12,0 | 5,0 | 3 |
Св. 140,0 до 160,0 включ. | 2,00 | 5,0 | 8,0 | 24 | 135,0 | 13,0 | 5,0 | 3 |
Св. 160,0 до 200,0 включ. | 2,50 | 6,0 | 9,0 | 24 | 160,0 | 13,0 | 6,0 | 3 |
Св. 200,0 до 240,0 включ. | 3,00 | 6,0 | 9,0 | 23 | 200,0 | 14,0 | 6,0 | 3 |
Св. 240,0 до 280,0 включ. | 3,50 | 7,0 | 10,0 | 22 | 235,0 | 14,0 | 7,0 | 3 |
Св. 280,0 | 4,00 | 8,0 | 12,0 | 22 | 250,0 | 14,0 | 8,0 | 3 |
Сварные соединения III категории | ||||||||
Св. 1,0 до 2,0 включ. | 0,10 | 0,4 | 0,6 | 12 | 0,8 | 5,0 | 0,5 | 2 |
Св. 2,0 до 3,0 включ. | 0,10 | 0,6 | 1,0 | 12 | 2,0 | 5,0 | 0,6 | 2 |
Св. 3,0 до 4,0 включ. | 0,20 | 0,8 | 1,2 | 12 | 3,5 | 5,0 | 0,8 | 2 |
Св. 4,0 до 5,0 включ. | 0,20 | 1,0 | 1,5 | 13 | 5,0 | 5,0 | 1,0 | 2 |
Св. 5,0 до 6,5 включ. | 0,20 | 1,2 | 2,0 | 13 | 6,0 | 5,0 | 1,2 | 3 |
Св. 6,5 до 8,0 включ. | 0,20 | 1,5 | 2,5 | 13 | 8,0 | 5,0 | 1,5 | 3 |
Св. 8,0 до 10,0 включ. | 0,30 | 1,5 | 2,5 | 14 | 10,0 | 5,0 | 1,5 | 3 |
Св. 10,0 до 12,0 включ. | 0,30 | 2,0 | 3,0 | 14 | 12,0 | 6,0 | 2,0 | 3 |
Св. 12,0 до 14,0 включ. | 0,40 | 2,0 | 3,0 | 15 | 14,0 | 6,0 | 2,0 | 3 |
Св. 14,0 до 18,0 включ. | 0,40 | 2,5 | 3,5 | 15 | 16,0 | 6,0 | 2,5 | 3 |
Св. 18,0 до 22,0 включ. | 0,50 | 3,0 | 4,0 | 16 | 20,0 | 7,0 | 3,0 | 3 |
Св. 22,0 до 24,0 включ. | 0,50 | 3,0 | 4,5 | 16 | 25,0 | 7,0 | 3,0 | 3 |
Св. 24,0 до 28,0 включ. | 0,60 | 3,0 | 4,5 | 18 | 25,0 | 8,0 | 3,0 | 3 |
Св. 28,0 до 32,0 включ. | 0,60 | 3,5 | 5,0 | 18 | 31,0 | 8,0 | 3,5 | 3 |
Св. 32,0 до 35,0 включ. | 0,60 | 3,5 | 5,0 | 20 | 35,0 | 9,0 | 3,5 | 3 |
Св. 35,0 до 38,0 включ. | 0,75 | 3,5 | 5,0 | 20 | 35,0 | 9,0 | 3,5 | 3 |
Св. 38,0 до 44,0 включ. | 0,75 | 4,0 | 6,0 | 21 | 41,0 | 10,0 | 4,0 | 3 |
Св. 44,0 до 50,0 включ. | 0,75 | 4,0 | 6,0 | 22 | 47,0 | 12,0 | 4,0 | 3 |
Св. 50,0 до 60,0 включ. | 1,00 | 4,0 | 6,0 | 23 | 55,0 | 14,0 | 4,0 | 4 |
Св. 60,0 до 70,0 включ. | 1,00 | 4,0 | 6,0 | 24 | 65,0 | 14,0 | 4,0 | 4 |
Св. 70,0 до 85,0 включ. | 1,25 | 5,0 | 7,0 | 25 | 78,0 | 14,0 | 5,0 | 4 |
Св. 85,0 до 100,0 включ. | 1,50 | 5,0 | 7,0 | 26 | 92,0 | 14,0 | 5,0 | 4 |
Св. 100,0 до 130,0 включ. | 2,00 | 5,0 | 8,0 | 27 | 115,0 | 14,0 | 5,0 | 4 |
Св. 130,0 до 165,0 включ. | 2,50 | 6,0 | 9,0 | 26 | 145,0 | 15,0 | 6,0 | 4 |
Св. 165,0 до 200,0 включ. | 3,00 | 6,0 | 9,0 | 25 | 160,0 | 15,0 | 6,0 | 4 |
Св. 200,0 до 225,0 включ. | 3,50 | 7,0 | 10,0 | 25 | 210,0 | 15,0 | 7,0 | 4 |
Св. 225,0 | 4,00 | 8,0 | 12,0 | 24 | 230,0 | 16,0 | 8,0 | 4 |
5.7.2.2 В таблице 8 требуемая чувствительность приведена для канавочных эталонов. При использовании проволочных эталонов значения чувствительности 0,30; 0,60; 0,75 и 1,5 мм допускается заменять на 0,32; 0,63; 0,80 и 1,6 мм соответственно.
5.7.2.3 Нормы допустимых одиночных включений и скоплений для сварных соединений Iн и IIн категорий деталей и сборочных единиц из стали приведены в таблице 9.
Таблица 9
Номинальная толщина сваренных деталей, мм | Требуемая чувстви- тельность, мм | Допустимый максимальный размер включения или скопления, мм | Допустимое количество включений и скоплений на любом участке сварного соединения длиной 100,0 мм, шт. | Допустимая суммарная приведенная площадь включений и скоплений на любом участке сварного соединения длиной 100,0 мм, мм |
Сварные соединения Iн категории | ||||
До 2,0 включ. | 0,10 | Не допускаются | Не допускаются | Не допускаются |
Св. 2,0 до 3,0 включ. | 0,10 | Не допускаются | Не допускаются | Не допускаются |
Св. 3,0 до 5,0 включ. | 0,10 | 0,4 | 3 | 0,5 |
Св. 5,0 до 8,0 включ. | 0,20 | 0,5 | 3 | 1,0 |
Св. 8,0 до 11,0 включ. | 0,30 | 0,6 | 4 | 1,5 |
Св. 11,0 до 14,0 включ. | 0,30 | 0,8 | 4 | 2,0 |
Св. 14,0 до 20,0 включ. | 0,30 | 1,0 | 4 | 3,0 |
Св. 20,0 до 26,0 включ. | 0,40 | 1,2 | 4 | 4,5 |
Св. 26,0 до 34,0 включ. | 0,40 | 1,6 | 4 | 7,0 |
Св. 34,0 до 45,0 включ. | 0,50 | 2,0 | 5 | 12,0 |
Св. 45,0 до 67,0 включ. | 0,60 | 2,5 | 5 | 20,0 |
Св. 67,0 до 90,0 включ. | 1,00 | 3,0 | 5 | 27,0 |
Св. 90,0 до 120,0 включ. | 1,25 | 4,0 | 5 | 45,0 |
Св. 120,0 до 200,0 включ. | 1,50 | 5,0 | 5 | 75,0 |
Св. 200,0 | 2,00 | 5,0 | 7 | 125,0 |
Сварные соединения IIн категории | ||||
До 2,0 включ. | 0,10 | Не допускаются | Не допускаются | Не допускаются |
Св. 2,0 до 3,0 включ. | 0,10 | 0,4 | 5 | 0,6 |
Св. 3,0 до 5,0 включ. | 0,20 | 0,5 | 5 | 1,0 |
Св. 5,0 до 8,0 включ. | 0,20 | 0,6 | 5 | 1,5 |
Св. 8,0 до 11,0 включ. | 0,20 | 0,8 | 5 | 2,5 |
Св. 11,0 до 14,0 включ. | 0,30 | 1,0 | 6 | 4,0 |
Св. 14,0 до 20,0 включ. | 0,30 | 1,2 | 6 | 6,0 |
Св. 20,0 до 26,0 включ. | 0,40 | 1,5 | 6 | 9,0 |
Св. 26,0 до 34,0 включ. | 0,50 | 2,0 | 6 | 16,0 |
Св. 34,0 до 45,0 включ. | 0,60 | 2,5 | 7 | 25,0 |
Св. 45,0 до 67,0 включ. | 0,75 | 3,0 | 7 | 36,0 |
Св. 67,0 до 90,0 включ. | 1,00 | 4,0 | 7 | 64,0 |
Св. 90,0 до 120,0 включ. | 1,25 | 5,0 | 7 | 100,0 |
Св. 120,0 до 200,0 включ. | 1,50 | 5,0 | 8 | 125,0 |
Св. 200,0 | 2,00 | 5,0 | 10 | 175,0 |
Примечание - Для сварных соединений вварки труб в трубные доски Iн, IIн категорий с номинальным диаметром трубы 16,0 мм нормы устанавливаются в конструкторской документации. 16,0 мм нормы устанавливаются в конструкторской документации. |
5.7.2.4 Включения, максимальный размер которых менее значений, указанных в графе "требуемая чувствительность" таблиц 8 и 9, не учитывают при подсчете количества включений и их суммарной приведенной площади и при рассмотрении расстояний между включениями (скоплениями).
5.7.2.5 При номинальной толщине стенки сваренных деталей менее 1,0 мм нормы допустимых одиночных включений устанавливаются конструкторской документацией; нормы не должны превышать значений, приведенных в таблицах 8 и 9 для толщины 1,0 мм.
5.7.2.6 При отсутствии одиночных крупных включений или при их количестве меньшем норм, приведенных в таблице 8, могут быть допущены в соответствующем количестве одиночные включения и (или) одиночные скопления допустимых размеров без учета при подсчете суммарной площади одиночных включений и одиночных скоплений.
5.7.2.7 Для сварных соединений (наплавленных кромок) протяженностью менее 100,0 мм нормы, приведенные в таблицах 8 и 9, по количеству и суммарной площади включений (скоплений) должны быть пропорционально уменьшены. Дробное количество допускаемых включений (скоплений) округляется до ближайшего целого числа.
5.7.2.8 При контроле предварительно наплавленных кромок требуемая чувствительность контроля и допустимые максимальные размеры одиночных включений и скоплений принимаются по нормам, приведенным в таблицах 8 и 9. Допустимое количество и суммарная приведенная площадь одиночных включений и скоплений не должны превышать 50% значений, приведенных в таблицах 8 и 9.
5.7.3 Алюминиевые сплавы
5.7.3.1 Нормы допустимых размеров одиночных включений и скоплений для сварных соединений I, II, III категорий деталей и сборочных единиц из алюминиевых сплавов приведены в таблице 10.
Таблица 10
Номинальная толщина сваренных деталей, мм | Требуемая чувствительность контроля, мм, не более | Допустимый максимальный размер, мм | Допустимый максимальный размер включений и скоплений для любого участка радиографического снимка длиной 100,0 мм, мм | |||
|
|
| категории сварных соединений | |||
|
| включения | скопления | I | II | III |
От 3,0 до 5,0 включ. | 0,1 | 1,0 | 1,8 | 4,0 | 6,0 | 10,0 |
Св. 5,0 до 8,0 включ. | 0,2 | 1,2 | 2,2 | 6,0 | 8,0 | 12,0 |
Св. 8,0 до 12,0 включ. | 0,3 | 1,5 | 2,5 | 8,0 | 10,0 | 15,0 |
Св. 12,0 до 18,0 включ. | 0,4 | 2,0 | 3,0 | 10,0 | 15,0 | 20,0 |
Св. 18,0 до 25,0 включ. | 0,5 | 2,5 | 4,0 | 12,0 | 18,0 | 24,0 |
Св. 25,0 до 30,0 включ. | 0,5 | 3,0 | 5,0 | 14,0 | 20,0 | 26,0 |
5.7.4 Титановые сплавы
5.7.4.1 Нормы допустимых размеров несплошностей сварных соединений деталей и сборочных единиц из титановых сплавов приведены в таблице 11.
Таблица 11
Номинальная толщина сваренных деталей, мм | Категория сварного соеди- нения | Требуемая чувстви- тельность контроля, мм, не более | Допустимый максимальный размер отдельной несплошности (поры и включения), мм | Допустимый суммарный максимальный размер всех допустимых несплошностей | |
|
|
|
| для любого участка радиогра- фического снимка длиной 100,0 мм, мм | для всего радиогра- фического снимка, % |
До 2,0 включ. | I, II | 0,1 | 0,2 | 0,6 | 0,5 |
III | 0,1 | 0,4 | 2,5 | 2,5 | |
Св. 2,0 до 3,0 включ. | I, II | 0,1 | 0,3 | 0,9 | 0,7 |
III | 0,1 | 0,6 | 4,5 | 4,0 | |
Св. 3,0 до 4,0 включ. | I, II | 0,1 | 0,4 | 1,2 | 1,0 |
III | 0,1 | 0,8 | 5,6 | 5,0 | |
Св. 4,0 до 5,0 включ. | I, II | 0,1 | 0,5 | 1,5 | 1,5 |
III | 0,1 | 1,0 | 7,0 | 7,0 | |
Св. 5,0 до 12,0 включ. | I, II | 0,2 | 1,2 | 2,4 | 2,0 |
III | 0,2 | 1,5 | 9,0 | 9,0 | |
Св. 12,0 до 20,0 включ. | I, II | 0,3 | 1,5 | 3,6 | 3,0 |
III | 0,4 | 2,0 | 13,0 | 13,0 | |
Св. 20,0 до 40,0 включ. | I, II | 0,5 | 2,0 | 6,0 | 5,0 |
III | 0,6 | 3,5 | 15,0 | 15,0 | |
Св. 40,0 до 100,0 включ. | I, II | 1,0 | 2,5 | 7,5 | 6,0 |
| III | 1,25 | 4,5 | 25,0 | 25,0 |
Примечания 1 При протяженности шва менее 100,0 мм контроль проводят по всей длине шва. 2 Скопления или цепочки пор или включений не допускаются. |
5.8 Оценка качества при ультразвуковом контроле
5.8.1 Общие требования
5.8.1.1 Качество сварного соединения, наплавки кромок под сварку считается удовлетворительным при одновременном соблюдении следующих требований:
а) значения характеристик и количество несплошностей удовлетворяют допустимым значениям для сварных соединений, приведенным в таблицах 12-14;
б) расстояние по поверхности сканирования между двумя соседними несплошностями - не менее условной протяженности несплошности с большим значением этого показателя;
в) отсутствие плоскостных несплошностей типа трещин и несплавлений с основным металлом.
5.8.2 Стали перлитного класса и высокохромистые стали
5.8.2.1 Нормы допустимых одиночных несплошностей при ультразвуковом контроле стыковых сварных соединений деталей и сборочных единиц с толщиной от 2,0 до 5,5 мм из сталей перлитного класса и (или) из высокохромистых сталей приведены в таблице 12.
Таблица 12
Номинальная толщина сваренных деталей, мм | Браковочный уровень чувствительности от опорного углового отражателя в виде зарубки (ширина высота), мм | Допустимое количество фиксируемых одиночных несплошностей на любом участке сварного соединения длиной 100,0 мм, шт. |
От 2,0 до 2,5 включ. | 1,0 0,4 | 4 |
Св. 2,5 до 3,5 включ. | 1,0 0,6 | 5 |
Св. 3,5 до 4,0 включ. | 1,0 0,8 | 5 |
Св. 4,0 до 4,5 включ. | 1,2 0,8 | 6 |
Св. 4,5 до 5,0 включ. | 1,2 1,0 | 6 |
Св. 5,0 до 5,5 включ. | 1,2 1,1 | 6 |
Примечания 1 Браковочный уровень чувствительности установлен применительно к контролю с использованием стандартного отражателя в виде зарубки. 2 Контроль с настройкой по другим отражателям допускается при условии соблюдения требований ГОСТ Р 50.05.02. 3 Контрольный уровень чувствительности (уровень фиксации) достигается увеличением чувствительности дефектоскопа на 6 дБ по сравнению с браковочным уровнем. 4 Допуск на размеры стандартного углового отражателя при изготовлении не должен превышать ±10%, перпендикулярность отражающей поверхности зарубки - 90°±1,0°. 5 Указанные нормы могут применяться с пьезоэлектрическими преобразователями, указанными в таблице 2 ГОСТ Р 50.05.02-2018. 6 Не допускаются протяженные и поперечные несплошности по ГОСТ Р 50.05.02. |
5.8.2.2 Нормы допустимых размеров одиночных несплошностей при ультразвуковом контроле сварных соединений деталей и сборочных единиц с толщиной более 5,5 мм из сталей перлитного класса и (или) из высокохромистых сталей приведены в таблице 13.
Таблица 13
Номинальная толщина сваренных деталей, мм | Эквивалентная площадь одиночных несплошностей, мм | Допустимое количество фикси- руемых одиночных несплошностей на любом участке сварного соединения длиной 100,0 мм, шт. | |||||||
| минимально фиксируемая | максимально допустимая |
| ||||||
| Категория сварного соединения | ||||||||
| I, Iн, IIн | II | III | I, Iн, IIн | II | III | I, Iн, IIн | II | III |
От 5,5 до 10,0 включ. | 2,0 | 2,5 | 3,5 | 4,0 | 5,0 | 7,0 | 4 | 5 | 7 |
Св. 10,0 до 20,0 включ. | 2,0 | 2,5 | 3,5 | 4,0 | 5,0 | 7,0 | 5 | 6 | 8 |
Св. 20,0 до 40,0 включ. | 2,0 | 2,5 | 3,5 | 4,0 | 5,0 | 7,0 | 6 | 7 | 9 |
Св. 40,0 до 60,0 включ. | 2,5 | 3,5 | 5,0 | 5,0 | 7,0 | 10,0 | 7 | 8 | 10 |
Св. 60,0 до 80,0 включ. | 3,5 | 5,0 | 7,5 | 7,0 | 10,0 | 15,0 | 7 | 9 | 11 |
Св. 80,0 до 100,0 включ. | 5,0 | 7,5 | 10,0 | 10,0 | 15,0 | 20,0 | 7 | 9 | 11 |
Св. 100,0 до 120,0 включ. | 5,0 | 7,5 | 10,0 | 10,0 | 15,0 | 20,0 | 8 | 10 | 12 |
Св. 120,0 до 200,0 включ. | 7,5 | 10,0 | 15,0 | 15,0 | 20,0 | 30,0 | 8 | 10 | 12 |
Св. 200,0 до 300,0 включ. | 15,0 | 20,0 | 25,0 | 30,0 | 40,0 | 50,0 | 9 | 11 | 13 |
Св. 300,0 до 400,0 включ. | 25,0 | - | - | 50,0 | - | - | 10 | - | - |
Св. 400,0 до 600,0 включ. | 35,0 | - | - | 60,0 | - | - | 10 | - | - |
Примечания 1 Не допускаются протяженные и поперечные несплошности по ГОСТ Р 50.05.02. 2 Нормы оценки качества по эквивалентной площади приведены применительно к контролю с использованием плоскодонного отражателя. 3 При контроле сварных соединений деталей и сборочных единиц из стали с номинальной толщиной стенки до 20,0 мм допускается использование угловых отражателей (зарубок), размеры которых рассчитывают с учетом норм допустимых одиночных несплошностей. 4 Контроль с настройкой по другим отражателям допускается при условии соблюдения требований ГОСТ Р 50.05.02. |
5.8.2.3 Предварительно наплавленные кромки контролируют в составе готового сварного соединения по нормам оценки качества, приведенным в таблице 13, без разделения на предварительную наплавку и металл шва.
Необходимость и объем промежуточного контроля предварительно наплавленных кромок, а также допускаемое число одиночных несплошностей, выявляемых при указанном контроле, устанавливаются проектной документацией.
При контроле сварных соединений труб с номинальной толщиной стенки до 20,0 мм допускается использование стандартного отражателя в виде зарубки и применение норм допустимых одиночных несплошностей, приведенных в таблице 13.
5.8.2.4 Нормы допустимых размеров одиночных несплошностей в зоне сплавления наплавленного металла с основным при контроле наплавленных аустенитными сварочными материалами покрытий и кромок деталей из сталей перлитного класса или из высокохромистых сталей приведены в таблице 14.
Таблица 14
Номинальная толщина основного металла с наплавленной кромкой, мм | Эквивалентная площадь одиночных несплошностей, мм | Допустимое количество фиксируемых одиночных несплошностей на любом участке наплавленной кромки длиной 100,0 мм, шт. | |||
| минимально фиксируемая | максимально допустимая | категория сварного соединения | ||
|
|
| I, Iн, IIн | II | III |
Св. 10,0 до 40,0 включ. | 3,5 | 7,0 | 3 | 4 | 5 |
Св. 40,0 до 60,0 включ. | 3,5 | 7,0 | 4 | 5 | 6 |
Св. 60,0 | 3,5 | 7,0 | 5 | 6 | 7 |
Примечание - Не допускаются протяженные и поперечные несплошности по ГОСТ Р 50.05.02. |
5.8.3 Алюминиевые сплавы
5.8.3.1 Нормы оценки качества по результатам ультразвукового контроля сварных соединений деталей и сборочных единиц из алюминиевых сплавов приведены в таблице 15.
Таблица 15
Толщина элемента контролируемого сварного соединения, мм | Минимально фиксируемая площадь одиночной несплошности, мм | Максимально допустимая эквивалентная площадь одиночной несплошности, мм | Максимально допустимое значение условной протяженности несплошности, мм |
Св. 6,0 до 10,0 включ. | 0,75 | 1,5 | 5 |
Св. 10,0 до 16,0 включ. | 0,75 | 1,5 | 10 |
Св. 16,0 до 20,0 включ. | 1,0 | 2,0 | 10 |
Св. 20,0 до 24,0 включ. | 1,0 | 2,0 | 20 |
Примечания 1 Браковочным уровнем чувствительности является максимально допустимая эквивалентная площадь несплошности. 2 Поисковый уровень чувствительности достигается увеличением чувствительности дефектоскопа на 6 дБ по сравнению с браковочным уровнем. 3 Условную протяженность несплошности измеряют по уменьшению амплитуды сигнала до поискового уровня чувствительности. 4 Указанные нормы могут применяться с пьезоэлектрическими преобразователями, указанными в таблице 2 ГОСТ Р 50.05.02-2018. |
5.8.4 Титановые сплавы
5.8.4.1 Допустимые значения эквивалентной площади несплошностей сварных соединений деталей и сборочных единиц из титановых сплавов приведены в таблице 16.
Таблица 16
Толщина элемента контролируемого сварного соединения, мм | Минимально фиксируемая площадь одиночной несплошности, мм | Максимально допустимая эквивалентная площадь одиночной несплошности, мм |
Св. 6,0 до 20,0 включ. | 1,5 | 3,0 |
Св. 20,0 до 40,0 включ. | 2,5 | 5,0 |
Св. 40,0 до 60,0 включ. | 3,5 | 7,0 |
Св. 60,0 до 100,0 включ. | 10,0 | 20,0 |
5.8.4.2 Допустимые значения условной протяженности несплошностей сварных соединений деталей и сборочных единиц из титановых сплавов приведены в таблице 17.
Таблица 17
Глубина залегания несплошности, мм | Максимально допустимая условная протяженность одиночной несплошности, мм |
До 20,0 включ. | 10,0 |
Св. 20,0 до 60,0 включ. | 20,0 |
Св. 60,0 до 100,0 включ. | 30,0 |
Примечания 1 Поперечные несплошности по ГОСТ Р 50.05.02 не допускаются вне зависимости от условной протяженности. 2 Указанные нормы могут применяться с пьезоэлектрическими преобразователями, указанными в таблице 2 ГОСТ Р 50.05.02-2018. |
5.8.4.3 Допустимое количество несплошностей при допустимых значениях эквивалентной площади и условной протяженности сварных соединений деталей и сборочных единиц из титановых сплавов приведены в таблице 18.
Таблица 18
Толщина элемента контролируемого сварного соединения, мм | Предельно допустимое количество одиночных несплошностей на участке шва длиной 100,0 мм, не более |
От 6,0 до 60,0 включ. | 3 |
Св. 60,0 до 100,0 включ. | 4 |
5.9 Оценка качества при вихретоковом контроле
5.9.1 Общие положения
5.9.1.1 Вихретоковый контроль проводят для оценки состояния металла теплообменных труб парогенератора РУ ВВЭР.
5.9.1.2 При организации контроля вихретоковым методом необходимо учитывать требования к проведению такого контроля, изложенные в [4].
5.9.2 Оценка качества металла теплообменных труб парогенератора
5.9.2.1 Нормы оценки состояния металла теплообменных труб по результатам вихретокового контроля установлены для несплошностей, ориентированных вдоль оси теплообменных труб.
5.9.2.2 При оценке качества теплообменных труб парогенератора не допускается несплошность металла теплообменных труб глубиной более 87% от номинальной толщины стенки теплообменных труб.
5.9.2.3 Несплошность металла теплообменных труб глубиной до 60% от номинальной толщины стенки теплообменных труб допускается независимо от ее протяженности.
5.9.2.4 Несплошности металла теплообменных труб с глубиной от 60% до 87% включительно допускаются в соответствии с таблицей 19 в зависимости от их протяженности.
Таблица 19
Допустимая глубина несплошности, % от номинальной толщины стенки | Протяженность несплошности, мм |
От 60 до 76 включ. | До 20 включ. |
Св. 76 до 87 включ. | До 5 включ. |
Примечание - Несплошности, расположенные на расстоянии менее 10,0 мм друг от друга, рассматриваются как одна протяженная несплошность. |
5.9.2.5 При использовании норм для оценки качества металла теплообменных труб по результатам вихретокового контроля должны быть соблюдены следующие условия:
б) максимально допустимая относительная погрешность измерения высоты и протяженности несплошности должна быть не более 20% для доверительной вероятности P=0,95;
г) соотношение сигнал/шум между сигналом от несплошности и объекта контроля должно быть не менее 2.
Минимальные размеры фиксируемых несплошностей при вихретоковом контроле теплообменных труб и перемычек коллекторов парогенератора указаны в ГОСТ Р 50.05.10.
5.9.2.6 В случае отсутствия измерительных средств контроля для получения данных о протяженности несплошностей металла теплообменных труб глубиной от 60% до 87% (включительно) допускается применять амплитудные критерии контроля в соответствии с таблицами 20-22 в зависимости от типа используемой аппаратуры. В таблице 20 приведены амплитудные критерии при контроле дефектоскопом HARMONIC-210 при нормировании 1,4 В на частоте 130 кГц, в таблице 21 амплитудные критерии при контроле дефектоскопами MIZ-70, MIZ-30, MIZ-85, OMNI-200 при нормировании 10,0 В на частоте 100 кГц, в таблице 22 - амплитудные критерии при контроле дефектоскопом TEDDY при нормировании 5,0 В на частоте 140 кГц.
Таблица 20
Допустимая глубина несплошности, % от номинальной толщины стенки теплообменных труб | Амплитуда сигнала на открытом участке теплообменных труб, В | Амплитуда сигнала под дистанционирующей решеткой, В |
От 60 до 68 включ. | Менее 0,63 | Менее 0,55 |
Св. 68 до 77 включ. | Менее 0,58 | Менее 0,50 |
Св. 77 до 87 включ. | Менее 0,38 | Менее 0,33 |
Таблица 21
Допустимая глубина несплошности, % от номинальной толщины стенки теплообменных труб | Амплитуда сигнала на открытом участке теплообменных труб, В | Амплитуда сигнала под дистанционирующей решеткой, В |
От 60 до 68 включ. | Менее 3,63 | Менее 3,16 |
Св. 68 до 77 включ. | Менее 3,33 | Менее 2,90 |
Св. 77 до 87 включ. | Менее 2,21 | Менее 1,92 |
Таблица 22
Допустимая глубина несплошности, % от номинальной толщины стенки теплообменных труб | Амплитуда сигнала на открытом участке теплообменных труб, В | Амплитуда сигнала под дистанционирующей решеткой, В |
От 60 до 68 включ. | Менее 1,64 | Менее 1,43 |
Св. 68 до 77 включ. | Менее 1,50 | Менее 1,31 |
Св. 77 до 87 включ. | Менее 1,00 | Менее 0,87 |
5.9.2.7 Оценка по амплитудному критерию проводится посредством нормирования от сигнала настроечного образца, поставляемого в комплекте с дефектоскопом:
- с тремя сквозными отверстиями диаметром 1,30 мм, расположенными в поперечном сечении под углом 120°, - для вихретоковых систем с дефектоскопами MIZ-30, MIZ-70, MIZ-85, OMNI-200;
- с четырьмя сквозными отверстиями диаметром 1,20 мм, расположенными в поперечном сечении под углом 90°, - для вихретоковых систем с дефектоскопом HARMONIC;
- с четырьмя плоскодонными отверстиями диаметром 4,75 мм, расположенными в поперечном сечении под углом 90°, - для вихретоковых систем с дефектоскопом TEDDY.
5.9.2.8 Применение амплитудного критерия для систем с дефектоскопами, не указанными в 5.9.2.6, возможно только при наличии специализированных методик контроля, прошедших оценку соответствия в форме испытаний и удовлетворяющих требованиям [3]. При этом данные методики должны содержать амплитудные критерии, соответствующие протяженностям и глубинам несплошностей, указанным в таблице 19.
6 Оценка качества антикоррозионных наплавок
6.1 Оценка качества при визуальном и измерительном контроле
6.1.1 На поверхности антикоррозионной наплавки допускаются одиночные включения размером не более 1,0 мм, если их количество на любом участке размером 100,0 х 100,0 мм не превышает четырех.
6.1.2 При проведении визуального контроля на поверхностях антикоррозионных наплавок включения с наибольшим фактическим размером до 0,2 мм не учитывают.
На поверхностях антикоррозионных наплавок высота (глубина) западания между валиками не должна превышать 1,0 мм, а чешуйчатость - 0,5 мм.
При автоматической дуговой наплавке лентой на поверхностях антикоррозионных наплавок допускается несовпадение высоты двух соседних валиков в местах их сопряжения не более 2,0 мм.
6.1.3 При измерениях толщины антикоррозионной наплавки на кромках деталей допустимые западания между валиками не учитывают.
6.1.4 Выявленные при визуальном и измерительном контроле несплошности, размеры которых превышают допустимые, должны быть устранены по технологической документации организации-изготовителя до проведения контроля другими методами.
6.2 Оценка качества при капиллярном контроле
6.2.1 Оценку качества антикоррозионной наплавки при капиллярном контроле проводят в соответствии с 5.5.
6.3 Оценка качества при ультразвуковом контроле
6.3.1 Качество антикоррозионной наплавки считается удовлетворительным при одновременном соблюдении следующих требований:
а) характеристики и количество несплошностей соответствуют допустимым значениям, приведенным в таблицах 25, 26;
б) расстояние по поверхности сканирования между двумя соседними несплошностями - не менее условной протяженности несплошности с большим значением этого показателя;
в) отсутствие плоскостных несплошностей типа трещин и несплавлений с основным металлом.
6.3.2 Нормы оценки качества зоны сплавления наплавленного металла с основным при контроле антикоррозионной наплавки приведены в таблице 23.
Таблица 23
Номинальная толщина наплавленной детали без учета покрытия, мм | Эквивалентная площадь одиночных несплошностей, мм | Допустимая суммарная эквивалентная площадь одиночных несплошностей на любом участке размером 200 200 мм, мм | |
| минимально фиксируемая | максимально допустимая |
|
До 100,0 включ. | 10,0 | 20,0 | 75,0 |
Св. 100,0 до 300,0 включ. | 15,0 | 30,0 | 100,0 |
Св. 300,0 | 20,0 | 40,0 | 125,0 |
6.3.3 По требованию конструкторской документации для деталей из стали марок 10ГН2МФА, 12Х2МФА, 12Х2МФА-А, 15Х2МФА, 15Х2МФА-А, 15Х2МФА мод.А, 15Х2МФА-А мод.А, 15X2МФА-А мод.Б, 15Х2НМФА, 15Х2НМФА-А, 15Х2НМФА класс 1, 15ХЗНМФА, 15ХЗНМФА-А, 15Х2НМ1ФА, 15Х2НМ1ФА-А с антикоррозионной наплавкой проводят ультразвуковой контроль поднаплавочной зоны шириной не менее 10,0 мм в целях выявления поднаплавочных трещин. Браковочный уровень чувствительности контроля устанавливается в соответствии с таблицей 24.
Таблица 24
Толщина наплавленного металла, мм | Браковочный уровень чувствительности. Диаметр плоскодонного отверстия, мм |
До 6,0 включ. | 2,0 |
Св. 6,0 до 11,0 включ. | 3,0 |
Св. 11,0 | 4,0 |
Примечания 1 Браковочный уровень чувствительности приведен применительно к контролю с использованием плоскодонного отражателя. 2 Указанные нормы могут применяться с пьезоэлектрическими преобразователями, применяемыми для выявления поднаплавочных трещин в соответствии с ГОСТ Р 50.05.02. |
Качество поднаплавочной зоны считается удовлетворительным, если не выявлены протяженные несплошности с амплитудой сигнала, превышающей браковочный уровень.
7 Оценка качества наплавленного металла уплотнительных и направляющих поверхностей
7.1 Оценка качества при визуальном и измерительном контроле
7.1.1 На уплотнительных поверхностях не допускаются округлые одиночные включения, размеры или количество которых превышают приведенные в таблице 25. Фиксации подлежат округлые одиночные включения с максимальным размером свыше 0,2 мм.
Включения с наибольшим размером до 0,2 мм включительно не учитываются.
Подлежащие фиксации включения не допускаются (вне зависимости от размеров и их количества), если:
а) они расположены на расстоянии менее 2,5 мм от границ рабочей поверхности;
б) хотя бы два включения расположены на одной радиальной линии (при плоском уплотнении) или на одной образующей (при конусном уплотнении).
Таблица 25
Номи- нальная ширина поверх- ности, мм | Максимально допустимый размер включения, мм | Максимально допустимое количество включений | |||||||
|
| на любом участке поверхности длиной 100,0 мм | на всей протяженности поверхности при , мм | ||||||
|
|
| до 65,0 | до 100,0 | до 150,0 | до 250,0 | до 400,0 | до 600,0 | св. 600,0 |
До 5,0 | Не допускаются (с учетом требований по фиксации несплошностей) | ||||||||
До 10,0 | 0,5 | 1 | 1 | 2 | 3 | 4 | 5 | 6 | 7 |
До 15,0 | 0,6 | 2 | 2 | 3 | 4 | 5 | 6 | 7 | 8 |
До 25,0 | 0,8 | 2 | 3 | 4 | 5 | 6 | 7 | 8 | 9 |
До 35,0 | 1,0 | 3 | 4 | 5 | 6 | 7 | 8 | 9 | 10 |
До 50,0 | 1,2 | 3 | 5 | 6 | 7 | 8 | 9 | 10 | 12 |
Св. 50,0 | 1,5 | 4 | 6 | 7 | 8 | 9 | 10 | 12 | 15 |
7.1.3 Для уплотнительных и прилегающих к ним боковых наплавленных поверхностей протяженностью менее 100,0 мм нормы по количеству допустимых включений должны быть пропорционально изменены. Дробное количество допускаемых включений округляется до ближайшего целого числа.
7.2 Оценка качества при капиллярном контроле
7.2.1 При капиллярном контроле оценку качества наплавленных поверхностей допускается проводить как по индикаторным следам, так и по фактическим характеристикам выявленных несплошностей после удаления проявителя в зоне зафиксированных индикаторных следов.
7.2.2 Результаты контроля по индикаторным следам считаются удовлетворительными при одновременном соблюдении следующих условий:
а) все индикаторные следы являются округлыми, линейные индикаторные следы отсутствуют;
б) наибольший размер каждого индикаторного следа не превышает трехкратной величины допускаемых значений, приведенных в 7.1.1, 7.1.2, 7.1.3 для одиночных включений;
в) количество индикаторных следов не превышает значений, приведенных в 7.1.1, 7.1.3 для одиночных включений;
г) индикаторные следы являются одиночными (минимальное расстояние между краями двух любых округлых индикаторных следов не меньше максимального размера большего из двух рассматриваемых следов).
Округлые индикаторные следы с наибольшим размером до 0,6 мм включительно не учитываются.
Несплошности, не соответствующие нормам настоящего пункта, должны быть подвергнуты контролю по фактическим характеристикам, приведенным в 7.1.1, 7.1.3. Результаты контроля являются окончательными.
7.3 Оценка качества при контроле твердости
7.3.1 Твердость наплавленного металла уплотнительных поверхностей деталей после термической обработки должна соответствовать значениям, приведенным в ГОСТ Р 50.05.25. Допускается отклонение значений твердости двухслойных наплавок от указанных в таблице значений не более чем на 8%.
7.3.2 Верхний допустимый предел твердости устанавливается конструкторской и технологической документацией с учетом значений, приведенных в ГОСТ Р 50.05.25 в зависимости от объема наплавленного металла и режимов термической обработки.
7.3.3 Количество замеров должно быть не менее:
а) двух - для арматуры с номинальным диаметром до 65,0 мм включительно;
б) трех - для арматуры с номинальным диаметром свыше 65,0 до 150,0 мм включительно;
в) пяти - для арматуры с номинальным диаметром свыше 150,0 до 400,0 мм включительно;
г) восьми - для арматуры с номинальным диаметром свыше 400,0 до 600,0 мм включительно;
д) десяти - для арматуры с номинальным диаметром свыше 600,0 мм.
7.3.4 При получении неудовлетворительных результатов измерения твердости наплавленных поверхностей допускается проведение повторных измерений с удвоенным количеством измерений. Результаты повторных измерений являются окончательными.
7.3.5 На деталях с наплавленными поверхностями, доступными для измерения твердости, контроль проводят непосредственно на рабочих поверхностях наплавленного металла после предварительной механической обработки с припуском на окончательную механическую обработку не более 0,5 мм.
7.3.6 На деталях с наплавленными поверхностями, недоступными для измерения твердости, контроль проводят на контрольных образцах, идентичных контролируемым производственным наплавленным деталям по марке основного металла, подготовке под наплавку, способу наплавки, партии наплавочных материалов, технологии выполнения наплавки, термической и механической обработке.
7.4 Контроль качества наплавки уплотнительных поверхностей деталей арматуры из титановых сплавов
7.4.1 Геометрические размеры наплавки подлежат контролю непосредственно после выполнения наплавки перед выполнением термической обработки.
7.4.2 Визуальный контроль следует проводить после выполнения наплавки и механической обработки с целью выявления пор и вольфрамовых включений на поверхности наплавленного металла, а также трещин на поверхности наплавленного металла и в зоне термического влияния.
На наплавленном металле и в зоне термического влияния трещины не допускаются. На окончательно обработанной поверхности не допускаются вольфрамовые включения, а также поры, размеры и количество которых превышают значения, приведенные в таблице 26.
Таблица 26
Диаметр условного прохода, мм | Допускаемый размер пор, мм, не более | Допускаемое количество пор, шт., не более |
До 50,0 включ. | Диаметр 0,3;
глубина 0,2 | 1 |
Св. 50,0 до 100,0 включ. |
| 2 |
Св. 100,0 |
| 3 |
7.4.3 Капиллярный контроль следует проводить после предварительной и после окончательной механической обработки с целью выявления трещин и пор, не обнаруженных при визуальном контроле.
7.4.4 Измерения твердости наплавленного металла проводят непосредственно на уплотнительной поверхности после предварительной механической обработки. Плоскость, на которой проводят измерение твердости, должна иметь припуск 1,5-2,0 мм. Допускается измерять твердость наплавленного металла на образцах, наплавленных вместе со штатными изделиями той же партией присадочного материала, на тех же режимах и на том же оборудовании. Измерения проводят на механически обработанной поверхности при высоте наплавленного металла не менее 4,0 мм. Твердость наплавленного металла должна составлять 350-430 HV. Количество измерений твердости должно быть не менее десяти. Из десяти измерений допускается не более трех выбросов. При большем количестве выбросов количество измерений удваивается, но допускается не более шести выбросов. Результаты измерения твердости на удвоенном количестве образцов являются окончательными.
Библиография
[1] | Федеральные нормы и правила в области использования атомной энергии НП-089-15 | Правила устройства и безопасной эксплуатации оборудования и трубопроводов атомных энергетических установок |
[2] | Федеральные нормы и правила в области использования атомной энергии НП-071-18 | Правила оценки соответствия продукции, для которой устанавливаются требования, связанные с обеспечением безопасности в области использования атомной энергии, а также процессов ее проектирования (включая изыскания), производства, строительства, монтажа, наладки, эксплуатации, хранения, перевозки, реализации, утилизации и захоронения |
[3] | Федеральные нормы и правила в области использования атомной энергии НП-105-18 | Правила контроля металла оборудования и трубопроводов атомных энергетических установок при изготовлении и монтаже |
[4] | Федеральные нормы и правила в области использования атомной энергии НП-084-15 | Правила контроля основного металла, сварных соединений и наплавленных поверхностей при эксплуатации оборудования, трубопроводов и других элементов атомных станций |
УДК 621.791:006:354 | ОКС 25.200 |
Ключевые слова: оценка соответствия, контроль, нормы оценки качества, сварное соединение, несплошность, изготовление, монтаж |