ФЕДЕРАЛЬНОЕ АГЕНТСТВО
ПО ТЕХНИЧЕСКОМУ РЕГУЛИРОВАНИЮ И МЕТРОЛОГИИ
НАЦИОНАЛЬНЫЙ СТАНДАРТ РОССИЙСКОЙ ФЕДЕРАЦИИ
ГОСТ Р
71837—
2024
Оптика и фотоника
РЕЗКА ЛАЗЕРНАЯ ТОНКОЛИСТОВЫХ МЕТАЛЛОВ И СПЛАВОВ
Технологический процесс
Издание официальное
Москва Российский институт стандартизации 2024
ГОСТ Р 71837—2024
Предисловие
1 РАЗРАБОТАН Обществом с ограниченной ответственностью «Лазеры и оптические системы» (ООО «ЛОС») и Обществом с ограниченной ответственностью «Лазерный центр» (ООО «Лазерный центр»)
2 ВНЕСЕН Техническим комитетом по стандартизации ТК 296 «Оптика и фотоника»
3 УТВЕРЖДЕН И ВВЕДЕН В ДЕЙСТВИЕ Приказом Федерального агентства по техническому регулированию и метрологии от 29 ноября 2024 г. № 1792-ст
4 ВВЕДЕН ВПЕРВЫЕ
Правила применения настоящего стандарта установлены в статье 26 Федерального закона от 29 июня 2015 г. № 162-ФЗ «О стандартизации в Российской Федерации». Информация об изменениях к настоящему стандарту публикуется в ежегодном (по состоянию на 1 января текущего года) информационном указателе «Национальные стандарты», а официальный текст изменений и поправок — в ежемесячном информационном указателе «Национальные стандарты». В случае пересмотра (замены) или отмены настоящего стандарта соответствующее уведомление будет опубликовано в ближайшем выпуске ежемесячного информационного указателя «Национальные стандарты». Соответствующая информация, уведомление и тексты размещаются также в информационной системе общего пользования — на официальном сайте Федерального агентства по техническому регулированию и метрологии в сети Интернет (www.rst.gov.ru)
© Оформление. ФГБУ «Институт стандартизации», 2024
Настоящий стандарт не может быть полностью или частично воспроизведен, тиражирован и распространен в качестве официального издания без разрешения Федерального агентства по техническому регулированию и метрологии
II
ГОСТ Р 71837—2024
Содержание
1 Область применения..................................................................1
2 Нормативные ссылки..................................................................1
3 Термины и определения...............................................................2
4 Общие требования ...................................................................3
5 Требования к технологическому процессу лазерной резки...................................7
6 Контроль качества...................................................................11
7 Требования безопасности.............................................................12
Приложение А (рекомендуемое) Оптимальные параметры и режимы технологического процесса лазерной резки ..........................................................14
Библиография........................................................................16
III
ГОСТ Р 71837—2024
НАЦИОНАЛЬНЫЙ СТАНДАРТ РОССИЙСКОЙ ФЕДЕРАЦИИ
Оптика и фотоника РЕЗКА ЛАЗЕРНАЯ ТОНКОЛИСТОВЫХ МЕТАЛЛОВ И СПЛАВОВ Технологический процесс Optics and photonics. Laser cutting of thin sheet metals and alloys. Technological process
Дата введения — 2025—03—01
1 Область применения
Настоящий стандарт устанавливает требования к технологическому процессу (ТП) лазерной резки тонколистовых металлов и сплавов на основе цветных металлов, с максимальной толщиной до 3,9 мм (далее — материалы) по ГОСТ 16523.
Настоящий стандарт распространяется на тонколистовые металлы и сплавы, применяемые в промышленности.
2 Нормативные ссылки
В настоящем стандарте использованы нормативные ссылки на следующие документы:
ГОСТ 8.657 Государственная система обеспечения единства измерений. Фотометрия импульсная. Термины и определения
ГОСТ 12.1.003 Система стандартов безопасности труда. Шум. Общие требования безопасности
ГОСТ 12.1.004 Система стандартов безопасности труда. Пожарная безопасность. Общие требования
ГОСТ 12.1.005 Система стандартов безопасности труда. Общие санитарно-гигиенические требования к воздуху рабочей зоны
ГОСТ 12.1.007 Система стандартов безопасности труда. Вредные вещества. Классификация и общие требования безопасности
ГОСТ 12.1.012 Система стандартов безопасности труда. Вибрационная безопасность. Общие требования
ГОСТ 12.1.019 Система стандартов безопасности труда. Электробезопасность. Общие требования и номенклатура видов защиты
ГОСТ 12.1.040 Система стандартов безопасности труда. Лазерная безопасность. Общие положения
ГОСТ 12.2.003 Система стандартов безопасности труда. Оборудование производственное. Общие требования безопасности
ГОСТ 12.3.002 Система стандартов безопасности труда. Процессы производственные. Общие требования безопасности
ГОСТ 12.4.026 Система стандартов безопасности труда. Цвета сигнальные, знаки безопасности и разметка сигнальная. Назначение и правила применения. Общие технические требования и характеристики. Методы испытаний
ГОСТ 5583 (ИСО 2046—73) Кислород газообразный технический и медицинский. Технические условия
ГОСТ 9293 (ИСО 2435—73) Азот газообразный и жидкий. Технические условия
Издание официальное
1
ГОСТ Р 71837—2024
ГОСТ 10157 Аргон газообразный и жидкий. Технические условия
ГОСТ 16523 Прокат тонколистовой из углеродистой стали качественной и обыкновенного качества общего назначения. Технические условия
ГОСТ ЕН 12626 Безопасность металлообрабатывающих станков. Станки для лазерной обработки
ГОСТ IEC 60825-1 Безопасность лазерной аппаратуры. Часть 1. Классификация оборудования и требования
ГОСТ Р 8.568 Государственная система обеспечения единства измерений. Аттестация испытательного оборудования. Основные положения
ГОСТ Р 8.654 Государственная система обеспечения единства измерений. Требования к программному обеспечению средств измерений. Основные положения
ГОСТ Р 8.674 Государственная система обеспечения единства измерений. Общие требования к средствам измерений и техническим системам и устройствам с измерительными функциями
ГОСТ Р 8.678 Государственная система обеспечения единства измерений. Формы оценки соответствия технических систем и устройств с измерительными функциями установленным требованиям
ГОСТ Р 58373 (ИСО 11145:2018) Оптика и фотоника. Лазеры и лазерное оборудование. Термины и определения
ГОСТ Р 71028 Оптика и фотоника. Оборудование на базе волоконных лазеров. Требования лазерной безопасности
ГОСТ Р ИСО 8573-1 Сжатый воздух. Часть 1. Загрязнения и классы чистоты
ГОСТ Р ИСО 9013 Резка термическая. Классификация резов. Геометрические характеристики изделий и допуски по качеству
СП 52.13330 «СНиП 23-05-95 Естественное и искусственное освещение»
СП 56.13330 «СНиП 31-03-2001 Производственные здания»
СП 60.13330 «СНиП 41-01-2003 Отопление, вентиляция и кондиционирование воздуха»
Примечание — При пользовании настоящим стандартом целесообразно проверить действие ссылочных стандартов (сводов правил) в информационной системе общего пользования — на официальном сайте Федерального агентства по техническому регулированию и метрологии в сети Интернет или по ежегодному информационному указателю «Национальные стандарты», который опубликован по состоянию на 1 января текущего года, и по выпускам ежемесячного информационного указателя «Национальные стандарты» за текущий год. Если заменен ссылочный документ, на который дана недатированная ссылка, то рекомендуется использовать действующую версию этого документа с учетом всех внесенных в данную версию изменений. Если заменен ссылочный документ, на который дана датированная ссылка, то рекомендуется использовать версию этого документа с указанным выше годом утверждения (принятия). Если после утверждения настоящего стандарта в ссылочный документ, на который дана датированная ссылка, внесено изменение, затрагивающее положение, на которое дана ссылка, то это положение рекомендуется применять без учета данного изменения. Если ссылочный документ отменен без замены, то положение, в котором дана ссылка на него, рекомендуется применять в части, не затрагивающей эту ссылку. Сведения о действии сводов правил целесообразно проверить в Федеральном информационном фонде стандартов.
3 Термины и определения
В настоящем стандарте применены термины по ГОСТ 8.657, ГОСТ Р 58373, а также следующие термины с соответствующими определениями.
3.1 лазерная резка; ЛР (laser cutting): Процесс получения сквозного реза в материале с использованием концентрированного лазерного излучения.
3.2 технология резки (cutting technology): Совокупность операций для получения реза.
3.3 резка (cutting): Операция по резке.
3.4 рез (cut): Результат операции резки.
3.5 скорость резки (cutting speed): Длина реза, выполненная в единицу времени.
3.6 ширина реза (cutting width): Ширина, полученная при резке и измеренная в необходимой части реза.
3.7 начало реза (cut beginning): Точка на разрезаемой детали, с которой начинается рез.
3.8 грат (burr): Излишек металла, застывший в нижней части реза.
2
ГОСТ Р 71837—2024
3.9
система транспортировки и фокусировки (лазерного) излучения; СТФИ (Нрк. система доставки излучения) [laser beam transport and focusing system; laser beam delivery system (deprecated)]: Часть лазерного оборудования (ЛТК, ЛТУ), объединяющая в единый блок или модуль систему транспортировки излучения и систему фокусировки лазерного излучения.
[ГОСТ Р 71764—2024, статья 9]
3.10 лазерная технологическая установка для резки; ЛТУ для резки (lasertechnological assembly for cutting): Лазерная технологическая установка, применяемая для процесса лазерной резки.
3.11
скважность импульсов лазерного излучения q; скважность: Отношение периода следования импульсов лазерного излучения к длительности импульса лазерного излучения.
[ГОСТ 24453-80, статья 31]
3.12 газовый поток (gas flow): Химическое вещество или комбинация химических веществ в газообразном состоянии, используемые для организации процесса резки.
4 Общие требования
4.1 ТП ЛР материалов включает в себя следующие этапы:
- подготовку технологического оборудования, ввод параметров ТП;
- подготовку и обработку материала (при необходимости);
- реализацию ЛР;
- контроль качества ЛР;
- финишные операции зачистки, шлифовки, химической обработки и т. д. (при необходимости).
4.2 В результате реализации ТП ЛР на материале должен быть получен рез, заданной в технологической документации (ТД) конфигурации.
4.3 ТП ЛР, как правило, применяют в отношении следующих материалов:
- сталь (оцинкованная, углеродистая, нержавеющая, легированная, жаропрочная, конструкционная, броневая);
- алюминий и алюминиевые сплавы;
- титан и титановые сплавы;
- медь, латунь, бронза;
- цветные и драгоценные металлы;
- редкоземельные металлические материалы;
- сплавы специального назначения: для микроэлектроники, атомной промышленности и т. д;
- другие металлы и сплавы.
Технологическая обоснованность выбора материала для ЛР приведена в таблице 1.
Таблица 1
Углеродистые стали | Нержавеющие стали | Алюминий и его сплавы | Титан и его сплавы | Медь и ее сплавы |
+ + + | + + + | + +1 | + + + | ++2 |
Примечания 1 Проблемой ЛР является низкий коэффициент поглощения лазерного излучения и высокая теплопроводность материала (лазерный пучок должен обладать достаточно высокой мощностью и при этом фокусироваться в минимальное по размерам пятно). 2 В данной таблице применимы следующие обозначения: + + + — предпочтительно; + +1 —удовлетворительно (возможен выбор механической или плазменной резки); + +2 — удовлетворительно. |
3
ГОСТ Р 71837—2024
4.4 Требования к помещениям
4.4.1 ТП ЛР следует осуществлять в условиях производственных помещений, оборудованных вентиляцией и отоплением в соответствии с требованиями СП 56.13330 и СП 60.13330, норм проектирования освещения по СП 52.13330, имеющих весь необходимый перечень оборудования для выполнения ТП ЛР, а также транспортирования обрабатываемых материалов, в том числе крупногабаритных деталей.
4.4.2 Производственные помещения должны соответствовать требованиям СП 56.13330, ГОСТ 12.1.005.
4.5 Требования к технологическому оборудованию, оснастке и материалам
4.5.1 Технологическое оборудование для ЛР должно соответствовать требованиям ГОСТ IEC 60825-1, ГОСТ ЕН 12626, ГОСТ 12.1.040, ГОСТ 12.2.003.
4.5.2 Управление ТП ЛР осуществляют изменением плотности мощности, частоты и длительности импульсов, величины скважности импульсного излучения, времени воздействия лазерного излучения, скоростью сканирования и перемещения пучка по поверхности.
Примечание — Значительное влияние на скорость ЛР оказывает поглощательная способность металлов и сплавов, зависящая от температуры поверхности, длины волны, поляризации и угла падения лазерного пучка на обрабатываемую поверхность, а поглощенная энергия лазерного излучения находится в зависимости от параметров парогазовой плазмы, возникающей как при непрерывном, так и при импульсном режиме лазерного излучения в процессе ЛР.
4.5.3 При проектировании и реализации ТП ЛР следует учитывать, что на параметры качества реза влияют: параметры ЛТУ, режимы ЛР, параметры материала, параметры СТФИ и системы подачи газа.
4.5.4 Требования к параметрам ЛТУ
4.5.4.1 ЛТУ, применяемые в ТП ЛР, должны соответствовать следующим требованиям:
- длина волны — должна быть подобрана исходя из наименьшей величины отражательной способности разделяемого материала;
- режим работы — преимущественно импульсный;
- поляризация — должна учитываться при работе с твердотельными лазерами;
- энергия в импульсе — от 0,01 до 3 мДж;
- средняя мощность — от 1 до 500 Вт;
- длительность импульса — от 100 фс до 350 нс;
- частота следования импульсов — от 1 Гц до 4 МГц;
- состав газовой смеси — в зависимости от вида резки: аргон, азот, кислород, воздух или их смеси;
- давление газовой смеси — от 0 до 8 атм.;
- плотность мощности на поверхности является производной от выбранного режима и параметров фокусировки лазерного излучения.
4.5.4.2 Требования к контролируемым параметрам ЛТУ в зависимости от материала, который режут (тип, толщина), конфигурации реза (линейный, криволинейный, отверстия), чистоты кромки, типа ЛР, скорости резания, в зависимости от типа изделия определяет технолог в соответствии с ТД на изделие.
4.5.4.3 Для реализации ТП ЛР следует использовать ЛТУ с достаточными энергетическими характеристиками для плавления или испарения материала, средства измерения, обеспечивающие контроль заданных технологических параметров режима ЛР. Следует учитывать, что в зависимости от плотности мощности лазерного излучения количество расплавленного материала, стационарная температура, скорости плавления и испарения материала будут различными.
4.5.4.4 Мощность ЛТУ должна соответствовать способу ЛР, виду металла или сплава, толщине материала и обеспечивать плотность мощности на поверхности обрабатываемого материала, обеспечивающую превышение порога как минимум плавления материала, а как максимум его испарения. Для достижения высокой точности, качества кромок реза при сложной геометрии профиля реза или при наличии тонких перемычек следует уменьшить мощность ЛТУ и работать в режиме многопроходного испарения. Следует контролировать и обеспечивать постоянство мощности ЛТУ в течение всего времени ЛР материала, поскольку указанный параметр влияет на стабильность качества резки. Достигаемая скорость позиционирования лазерного пучка — до 300 м/мин, точность реза — до 0,005 мм.
4
ГОСТ Р 71837—2024
4.5.4.5 Рекомендуемые максимальные значения толщины обрабатываемого материала в зависимости от мощности ЛТУ приведены в таблице 2.
Таблица 2
Мощность ЛТУ, кВт | Рекомендуемая максимальная толщина обрабатываемого материала в зависимости от мощности ЛТУ, мм | ||||
Углеродистая сталь | Нержавеющая сталь | Алюминий и его сплавы | Титан и его сплавы | Медь и ее сплавы | |
0,5—1,0 | 0,2—7,0 | 0,5—2,0 | 0,2—1,5 | 0,5—1,5 | 0,2—1,0 |
2,0 | Св. 3,9 | Св. 3,9 | 3,0 | Св. 3,9 | 3,0 |
4.5.4.6 Контролируемые параметры режима ЛР включают в себя: скорость резки, вид газа, давление газа, положение фокуса по отношению к поверхности материала.
4.5.4.7 Учитываемые в ТП ЛР параметры материала включают: его толщину, геометрию и состояние поверхности, вид металла или сплава, из которого он изготовлен. При отработке ТП ЛР следует контролировать величины зоны термического влияния на материал металлографическим методом и методом измерения микротвердости в зоне входа реза, в зоне прямолинейного реза и на выходе лазерного пучка.
4.5.4.8 Параметры СТФИ и системы подачи газа определяет технолог исходя из положения выводимого лазерного пучка, астигматизма, отклоняющего зеркала, регулировки лазерного пучка относительно сопла, параметров отверстия сопла.
4.5.4.9 Мощность лазера, скважность импульсов и скорость резки следует подбирать при разработке параметров ТП согласованно, исходя из соответствия друг другу при условии получения необходимого уровня качества кромок реза. Полученное сочетание параметров ТП должно обеспечивать достижение контролируемого процесса удаления материала. Слишком высокая или слишком низкая скорость резки по отношению к оптимальной может привести к увеличению шероховатости кромок реза и образованию грата. Скорость резки уменьшается с увеличением толщины материала.
4.5.4.10 Непрерывный режим лазерного излучения, как правило, используют для резки контура металла без высоких требований к точности и качеству реза. Для газолазерной резки тонколистовых сталей по криволинейному контуру следует использовать непрерывное и импульсно-периодическое излучение, то есть лазерную установку, работающую в непрерывном и импульсном режимах. Для формирования отверстий или получения точных контуров реза следует использовать низкочастотные импульсные лазерные установки. Производительностью и качеством кромок реза следует управлять изменением технологического параметра — частоты импульсно-периодического лазерного излучения.
4.5.4.11 Применяемыми типами лазерных излучателей для ЛР являются:
- газовые, в которых активной средой является смесь различных газов, например углекислого газа, азота, водорода;
- твердотельные, в которых активной средой является кристалл, например алюмо-иттриевый гранат, легированный ионами неодима (Nd:YAG);
- волоконные, в которых оптический тракт и, возможно, резонатор являются элементами оптического волокна. Применяют цельноволоконные лазеры при полностью волоконной реализации и комбинированные волоконно-дискретные или гибридные при использовании волоконных и других элементов конструкции.
Технологическое оборудование и оснастка ЛТУ для резки должны быть взаимосвязаны, синхронизированы и автоматизированы полностью или частично. Технологическое оборудование должно обеспечивать стабильность основных параметров режимов ТП ЛМ, возможность их регулирования и контроля.
Технологическая оснастка должна быть изготовлена из негорючих материалов, обеспечивать надежное крепление обрабатываемого материала и точность его позиционирования в соответствии с требованиями ТД.
4.5.4.12 Технологическое оборудование и оснастка должны исключать выход отраженного (диффузного или зеркального) лазерного излучения за пределы зоны обработки.
5
ГОСТ Р 71837—2024
4.5.4.13 Для ЛР материалов применяют следующие виды технических газов:
- воздух высокой очистки по ГОСТ Р ИСО 8573-1 (используют, как правило, для ЛР металлов и сплавов толщиной до 1,5 мм; рекомендуемые классы чистоты воздуха по твердым частицам не ниже 3, по влажности и содержанию воды в жидкой фазе не ниже 5, по общему содержанию масел не ниже 2);
- кислород технический по ГОСТ 5583 (используют, как правило, для ЛР черных металлов, меди; требуемая чистота газа не менее 99,95 %);
- азот технический по ГОСТ 9293 (используют для ЛР всех цветных металлов и сплавов в любом диапазоне толщин, а также для резки черных металлов, если требуется защита от окислов; требуемая чистота газа не менее 99,995 %);
- аргон по ГОСТ 10157 (используют для ЛР титана и титановых сплавов);
- гелий газообразный сжатый (используют для ЛР титана и титановых сплавов);
- другие газы и смеси газов (например, смесь углекислого газа, азота, водорода для обработки сплавов на основе меди).
Поток газа высокого давления применяют для удаления паров и частиц материала, получаемых при ЛР, охлаждения кромок реза, а также для защиты линзы ЛТУ для резки и собственно фокусирующего устройства от попадания частиц материала.
4.6 Требования к поверхностям материала
4.6.1 Перед началом ТП ЛР на поверхности материала должны быть созданы условия для наилучшего поглощения лазерного излучения, которые зависят от длины волны используемой ЛТУ, плотности мощности лазерного излучения, частоты и длительности импульсов.
4.6.2 На подготовленных к ЛР поверхностях материала не должно быть следов коррозии, грязи, масла, краски, дефектов в виде вскрытых пор, раковин, трещин, прожогов, заусенцев.
4.7 Требования к параметрам технологического процесса лазерной резки
4.7.1 В зависимости от материала, его толщины, требований к чистоте реза, наличия подложки, скорости резки технолог определяет тип ТП ЛР и соответствующее оборудование для его осуществления. Далее задают параметры резки, которые на данном оборудовании могут варьироваться.
4.7.2 При разработке ТП ЛР разработчик должен определить настройки параметров ЛР путем выполнения пробной операции, комбинируя варианты сочетаний параметров: мощности и длины волны лазерного излучения, частоты и длительности импульсов, фокусного расстояния, скважности импульсов, постоянства мощности, поперечного сечения лазерного пучка, расходимости, поляризации, скорости резки, точности позиционирования лазерного излучения, вида режущего газа и давления его подачи. Выбранная комбинация параметров ТП должна обеспечить требуемое качество кромок реза при приемлемой скорости резания и энергетической эффективности ЛР для заданного вида материала, толщины материала и состояния поверхности материала.
4.7.3 При выполнении экспериментального подбора оптимальных режимов ТП ЛР выполняют следующие действия:
- формируют требования к качеству ЛР, желаемые размеры, форму и характеристики изделия, получаемого из материала в процессе ЛР;
- с использованием графического и лазерного программного обеспечения для автоматизированного проектирования формируют техническую модель обработки материала, с указанием необходимых размеров, углов, радиусов и кривых перемещения лазерного пучка, необходимых для получения желаемого результата ЛР с учетом требований технологичности и производственных ограничений;
- переводят техническую модель в машиночитаемые инструкции с помощью программного обеспечения ЛТУ, при этом задают необходимую траекторию обработки и соответствующую точку привязки с использованием системы числового программного управления для регистрации условий подачи по каждой оси и координатам точки привязки;
- подготавливают оборудование для ЛР, выбирают комбинацию параметров ЛТУ; лазерной установки, включая длину волны излучения, мощность ЛТУ, скважность импульсов, направление поляризации, скорость реза, фокусное расстояние, вид режущего газа и давление его подачи, а также другие параметры, перечисленные ранее;
- контролируют ТП ЛР и проверяют тестовый образец на точность и качество поверхностей реза, соответствие полученного результата и графической модели;
6
ГОСТ Р 71837—2024
- вносят коррективы в параметры настройки ЛТУ и определяют оптимальное сочетание параметров ТП, которое позволяет получить необходимое соответствие требованием ТД по точности и качеству поверхностей реза с приемлемыми значениями скорости реза и энергетической эффективности;
- определяют потребность в финишной обработке полученной заготовки, такой как зачистка, шлифовка, галтовка, химическая обработка и т. д.
4.7.4 Оптимальные параметры и режимы ТП ЛР приведены в приложении А.
4.8 Требования к производственному персоналу
К работе на лазерном технологическом оборудовании допускаются лица не моложе 18 лет, прошедшие практическую подготовку по работе на оборудовании при проведении ЛР и инструктаж по технике безопасности при работе на электроустановках, а также при работе с источниками лазерного излучения, в соответствии с инструкциями по технике безопасности, внедренными на предприятии.
5 Требования к технологическому процессу лазерной резки
5.1 Общие положения
5.1.1 ТП ЛР выполняют по ТД, разработанной на основании КД и настоящего стандарта.
5.1.2 В ТД должен быть установлен технологический режим ЛР — совокупность параметров ТП ЛР. Значения параметров ТП ЛР должны быть установлены в ТД.
5.2 Способы реализации технологического процесса лазерной резки
5.2.1 ЛР материалов выполняется как термический процесс, при котором сфокусированный лазерный пучок переносит энергию, требуемую для их резки.
В ряде случаев ТП ЛР может сопровождаться поддувом газа с различной скоростью, давлением и направлением газовой струи.
Примечание — Применение поддува газа зависит от типа используемой ЛР и характеристик разрезаемого материала.
5.2.2 Лазерный пучок и струю газа одновременно направляют в зону резки, при этом подаваемый газ осуществляет удаление расплавленного металла за пределы реза, оказывает влияние на такие параметры резки, как геометрия реза, наличие грата, охлаждение зоны резания и другие. Также вспомогательный газ может подаваться в герметичный резервуар, внутри которого происходит ЛР, формируя тем самым специальную газовую среду.
Процесс ЛР проводится на всю глубину разрезаемого материала, в движении, по направлению рабочего хода. Также резка может быть осуществлена с любой глубиной реза и с несколькими проходами лазерного излучения по одной зоне реза. Количество повторов регулируется в зависимости от достижения факта разделения материала.
5.2.3 Общая схема реализация ТП ЛР материалов приведена на рисунке 1.
7
ГОСТ Р 71837—2024
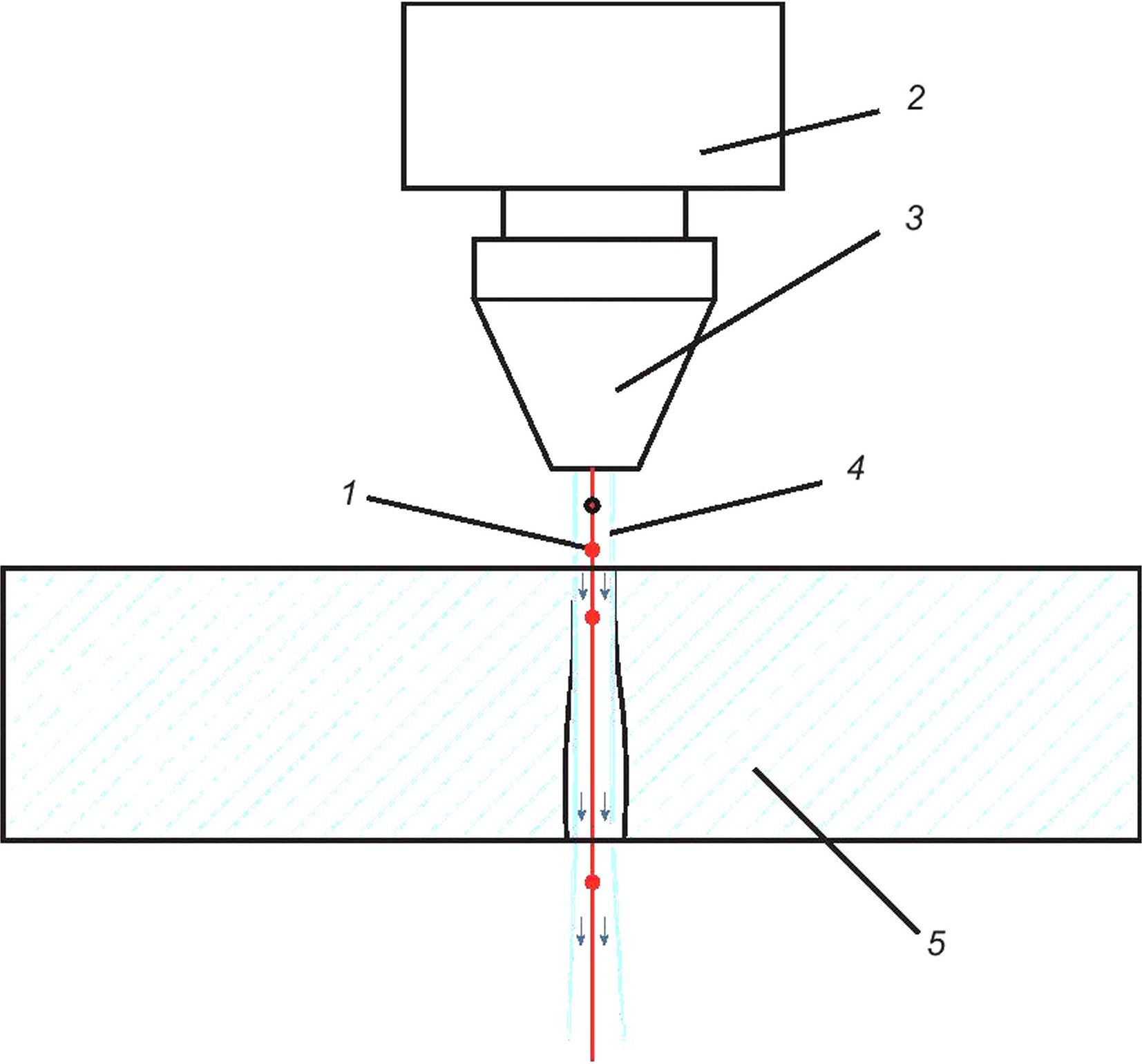
1 — лазерный пучок; 2 — лазерная установка; 3— сопло; 4 — струя газа; 5 — металл или сплав а — пример системы вертикального распространения лазерного излучения
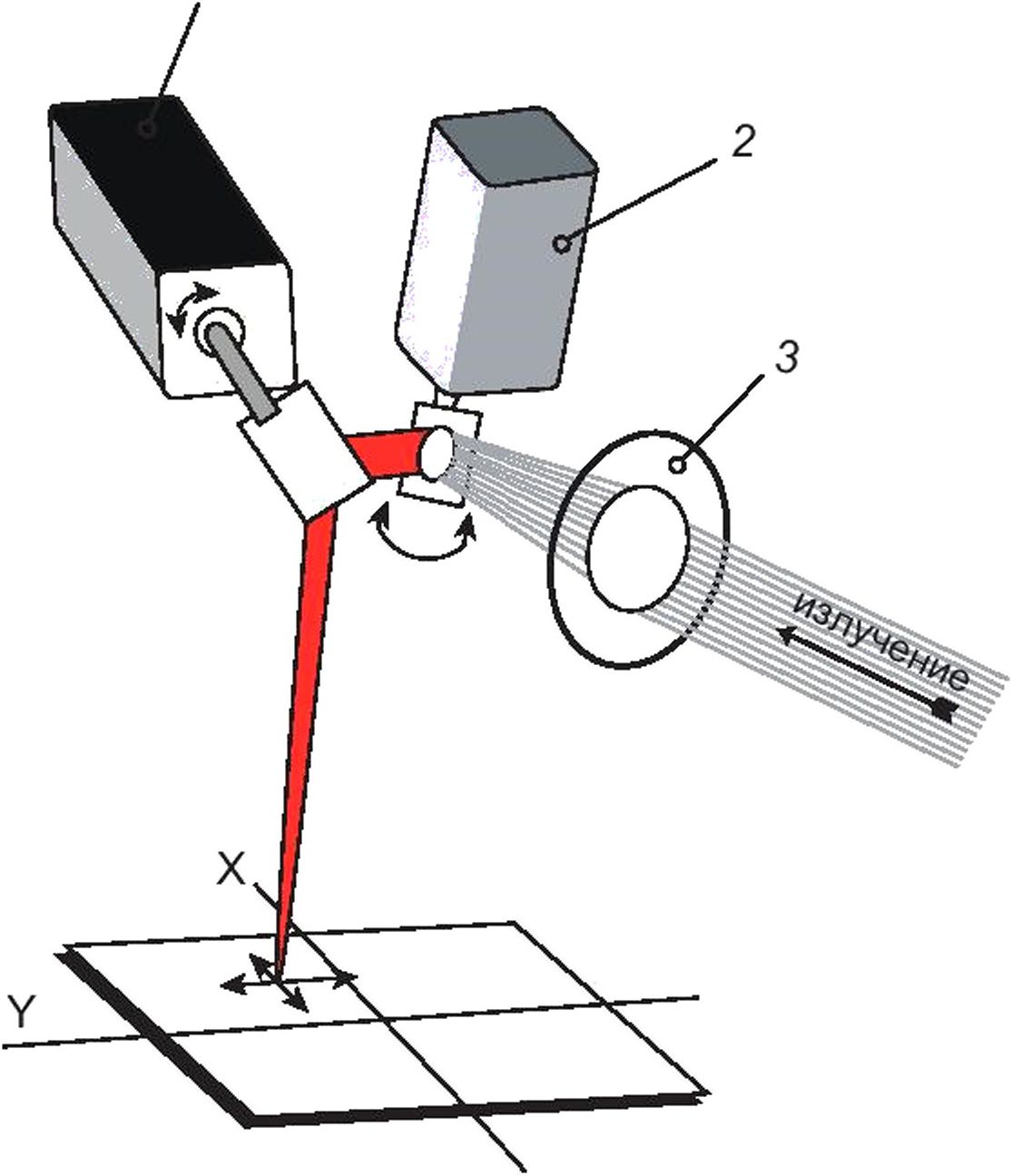
1 — У-сканатор; 2 — Х-сканатор; 3 — фокусирующая линза
б — пример системы сканирующего наведения лазерного излучения в зону ЛР материала Рисунок 1 — Общая схема реализация ТП ЛР материалов
Элементы ЛТУ и параметры ЛР приведены на рисунке 2.
8
ГОСТ Р 71837—2024
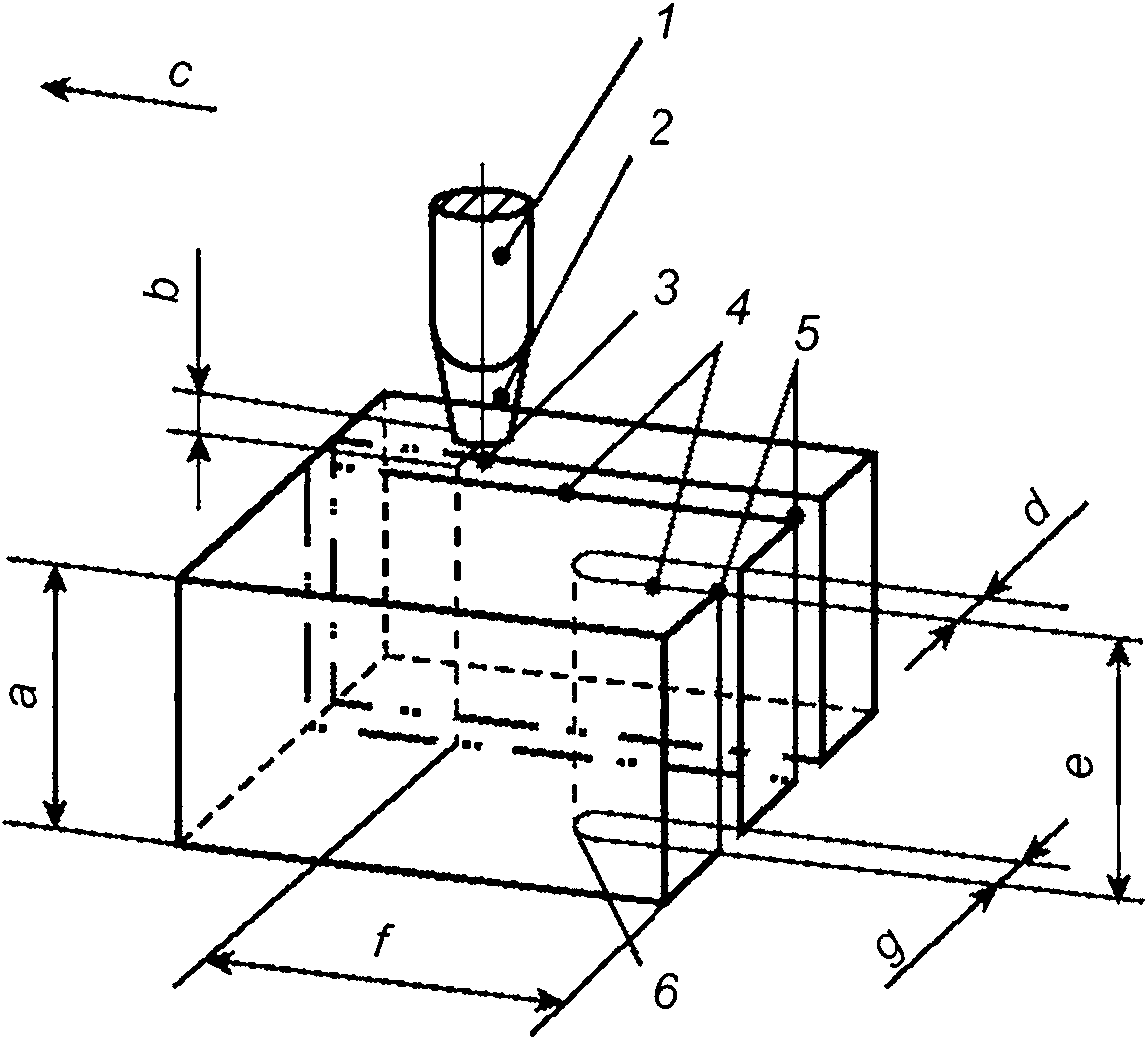
1 — лазерное устройство; 2 — сопло; 3 — лазерный пучок; 4 — рез; 5 — начало реза; 6 — конец реза; а — толщина детали; b — расстояние от сопла до поверхности материала; с — направление рабочего хода; d— ширина реза в верхней части; е — толщина реза; f— длина реза; д — ширина реза в нижней части; h — направление режущей струи
Рисунок 2 — Элементы ЛТУ и параметры ЛР
5.2.4 ЛР материалов может быть осуществлена следующими способами:
- испарительная (сублимационная) ЛР;
- испарительная ЛР с подачей вспомогательного газа или в газовой среде;
- ЛР плавлением с продувкой инертным газом или в газовой среде;
- ЛР плавлением с продувкой воздухом или техническим кислородом с организацией экзотермической реакции (реактивная резка).
При выборе способа ЛР следует принимать во внимание характеристики обрабатываемого материала, его толщину, изначальное качество поверхности и ее кривизну, требуемый уровень качества кромки реза.
5.2.5 Испарительная (сублимационная) ЛР выполняется как термический процесс, при котором рез формируется путем выпаривания материала в зоне резки, а продукты выпаривания выдуваются из щели реза путем естественного расширения пара, удаления высокоскоростной газовой струей или под действием давления паров отдачи. Для реализации данного способа локальное повышение температуры до точки испарения должно происходить настолько быстро, чтобы жидкий материал не успевал проявить свои гидродинамические свойства и скопиться в зоне реза.
При испарительной ЛР в большинстве случаев подводится лазерное импульсно-периодическое излучение. Частота, продолжительность и энергия лазерного импульсно-периодического излучения должны быть рассчитаны технологом из необходимости обеспечения испарения заданного участка материала на необходимую глубину. Данный способ требует существенного тепловвода и использования излучения с пико- и фемтосекундной длительностью импульсов. При этом мощность излучения влияет не только на характер процесса, но и на его производительность.
Данный вид ЛР применяют в основном для повышения качества реза за счет скорости, а также при необходимости сохранения материала подложки (при ее наличии) или для выполнения реза сложной пространственной формы, в том числе и при наличии перемычек. Для обеспечения минимальной ширины реза следует обеспечить высокую мощность и концентрацию излучения, что позволяет снизить потери качества, связанные с теплопроводностью разрезаемого материала.
Испарительную ЛР выбирают в случае необходимости обеспечить высокое качество реза, сохранение материала подложки (при ее наличии), гладкие кромки реза, минимальное термическое воздействие на материал, отсутствие окисления кромок реза. При этом следует учитывать недостатки данного способа, к которым относятся относительно низкая скорость резки и ограничения по толщине материала.
Испарительную ЛР применяют для материалов толщиной не более 1 мм, причем используемая длительность импульсов (фемтосекунды) обеспечивает работу в квазинепрерывном режиме. Диаметр сфокусированного лазерного пятна на обрабатываемом материале — от 2 до 60 мкм.
9
ГОСТ Р 71837—2024
5.2.6 При испарительной ЛР с подачей вспомогательного газа применяют инертные или химически пассивные газы (азот, гелий, аргон).
5.2.7 ЛР плавлением применяют при обработке всех металлов и сплавов. В процессе ее реализации рез формируется путем расплавления металлов и окислов в зоне резки, а продукты плавления выдуваются из щели реза высокоскоростной газовой струей (гелием, аргоном, азотом). Процесс позволяет применять более высокие скорости резки и требует введения меньшего количества энергии, так как удаление материала из зоны реза осуществляется не за счет испарения, как при сублимационной резке, а за счет удаления материала в жидкой фазе высокоскоростной газовой струей, динамическое воздействие которой превышает вязкокапиллярную силу расплава. При этом перемещение жидкой ванны расплава осуществляется вдоль канала реза с помощью постоянного притока энергии лазерного излучения и динамического воздействия газовой струи. Процесс выноса жидкой ванны расплава газовой струей может носить стационарный характер при равенстве скорости плавления и скорости удаления материала, и нестационарный характер при различии указанных скоростей.
Следует учитывать, что ЛР плавлением с подачей газовой струи под давлением свыше 0,6 МПа позволяет увеличить скорость удаления расплавленного материала из зоны реза, что предотвращает образование грата на кромках реза. Для предотвращения окисления кромок реза в качестве газа следует использовать азот или аргон. ЛР плавлением с высоким давлением газа используют, в основном, для нержавеющей стали и сплавов алюминия толщиной от 1 мкм до 1 мм.
Общие требования к газам для ЛР плавлением (режущим газам) должны соответствовать 4.5.4.13. Следует учитывать, что кроме удаления продуктов разрушения материала из зоны реза, продувка газовой струей позволяет обеспечить охлаждение кромок реза и снизить тепловые деформации. Такой же эффект достигается при использовании жидкой среды для охлаждения поверхности обрабатываемого материала.
При использовании СО2-лазера путем выбора параметров ТП ЛР может быть реализован режим плазменной резки, при котором формируется плазменное облако из ионизированного пара металла и ионизированного газа для резки, поглощающее энергию СО2-лазера, что увеличивает подвод тепла в зону резки и увеличивает скорость резки.
5.2.8 ЛР плавлением с продувкой воздухом или техническим кислородом (реактивная резка) выполняется как быстрый окислительный экзотермический процесс с участием высокой энергии лазера и с дополнительным тепловводом от химической реакции металла с кислородом. При этом учитывают, что окислительная реакция при процессе горения металла и сплава в кислороде дает в 3—5 раз больший объем тепла, подводимого в зону реза, чем лазерный пучок. При использовании данного способа ЛР может быть выбран режим нагрева непрерывным или импульсно-периодическим лазерным излучением до плавления металла или сплава, или режим нагрева до температуры наступления химической реакции окисления материала в среде кислорода. Следует учитывать, что применение данного способа ЛР позволяет снизить энергопотребление, увеличить скорость резки, однако, качество поверхностей реза при этом может снизиться.
При необходимости улучшить качество и энергетическую эффективность ТП ЛР, как правило, применяют импульсно-периодическое лазерное излучение. Выбор оптимальных параметров импульснопериодического лазерного излучения зависит от необходимого качества кромки реза и производительности процесса.
Примечание — ЛР плавлением с продувкой техническим кислородом используют, как правило, для резки черного металла1), исключая высоколегированные стали; не применяют для резки цветных металлов, исключая медь.
5.2.9 Способы ЛР для различных материалов приведены в таблице 3.
1) В настоящем стандарте термин «черный металл» применен для обозначения сталей, ферросплавов и чугунов.
10
Таблица 3
ГОСТ Р 71837—2024
Способ ЛР | Тепловвод в зону реза | Удаляемая фаза | Механизм удаления продуктов разрушения | Тип режима работы лазера | Материал |
Испарительная без продува | Лазерный пучок | Пары материала | За счет естественного расширения пара | Импульснонепрерывный | Медь, материалы толщиной до 1 мм |
Испарительная с продувом | Лазерный пучок | Пары материала | За счет естественного расширения пара и поддува | Импульснонепрерывный | Металлы толщиной до 1 мм |
Плавлением с продувкой инертным газом или в газовой среде | Лазерный пучок | Расплав материала | Газовой струей давлением свыше 0,6 МПа | Импульснонепрерывный и непрерывный | Нержавеющие стали, прочие металлы и сплавы |
Плавлением с продувкой кислородом или воздухом | Лазерный пучок и экзотермическая реакция | Расплав материала | Газовой струей давлением свыше 0,6 МПа | По выбору оператора ЛТУ | Черные металлы, нержавеющие стали, прочие металлы и сплавы |
5.2.10 Технологические преимущества ЛР перед другими способами резки и ее применение предпочтительно в случае необходимости обеспечить:
- отсутствие расходных материалов;
- быстро программируемые траектории реза;
- высокую автоматизацию процесса, позволяющую получать контуры сложных пространственных форм;
- комплексный подход, позволяющий за одну установку детали осуществить не только ЛР, но и закалку, маркировку, перфорацию, очистку и т. д.;
- малую ширину реза, которая обеспечивается локальным тепловым воздействием на поверхность разделяемого материала;
- отсутствие физического контакта с материалом и механического воздействия, что позволяет обрабатывать тонкие, легко деформируемые материалы;
- минимизацию термических деформаций;
- низкие потери материала;
- сложные, повторяемые контуры реза с высоким качеством поверхности в зоне реза;
- относительно высокую скорость резки;
- возможность точного контроля температуры нагрева в зоне реза;
- выполнение как плоской, так и трехмерной резки, возможность формирования шаровых и разъемных соединений;
- минимальную потребность в финишных операциях.
5.2.11 При использовании ЛР необходимо учитывать следующие особенности ее применения:
- высокое энергопотребление;
- необходимость удаления загрязненного воздуха из зоны реза и окружающей среды;
- требуемый высокий уровень квалификации операторов;
- учет отражательной способности разрезаемого материала.
6 Контроль качества
6.1 Требования к качеству ЛР материалов устанавливают в ТД в соответствии с ГОСТ Р ИСО 9013.
6.2 Контролируемые параметры качества ЛР по ГОСТ Р ИСО 9013 включают:
- допуск перпендикулярности или наклона кромки реза;
11
ГОСТ Р 71837—2024
- высоту элемента профиля, равную сумме значений высоты пика и глубины впадины элемента профиля;
- среднюю высоту профиля, равную среднему арифметическому значению пяти высот элементов профиля, граничащих между собой;
- оплавление верхней кромки, под которой понимают величину, характеризующую форму верхней кромки реза;
- размеры грата или облоя;
- выхваты, под которыми понимаются задиры или надрезы непостоянной ширины, глубины и очертаний, нарушающие однородную поверхность реза и образующиеся преимущественно в направлении режущей струи;
- размер зоны термического влияния обработанного материала, определяемый металлографическим методом и методом измерения микротвердости;
- изменение цвета металла в результате перегрева материала;
- наличие коррозии, окислов и других негативных последствий ЛР.
6.3 Качество ЛР обеспечивают путем выбора оптимальных технологических параметров ТП ЛР по 4.7.2.
6.4 Качество ЛР контролируют методами, установленными в нормативной документации (КД, ТД) для конкретного типа материала.
6.5 Применяемые средства измерений должны быть поверены или калиброваны в установленном порядке.
6.6 Эталоны единиц величин должны быть аттестованы.
6.7 Стандартные образцы должны иметь утвержденный тип и соответствовать установленному сроку службы.
6.8 Испытательное оборудование должно быть аттестовано в соответствии с ГОСТ Р 8.568; средства измерений, используемые в составе испытательного оборудования, должны быть поверены.
6.9 Средства контроля и индикаторы, являющиеся техническими средствами, должны быть проверены на соответствие эксплуатационной документации.
6.10 Программное обеспечение средств измерений должно соответствовать требованиям ГОСТ Р 8.654.
6.11 Технические системы и устройства с измерительными функциями должны соответствовать требованиям ГОСТ Р 8.674 и ГОСТ Р 8.678.
7 Требования безопасности
7.1 Требования безопасности при осуществлении ТП ЛР — по ГОСТ 12.3.002 и в соответствии с инструкциями по охране труда предприятия.
7.2 Требования безопасности к конструкции и эксплуатации лазерного технологического оборудования — по ГОСТ IEC 60825-1, ГОСТ ЕН 12626, ГОСТ 12.1.040, ГОСТ Р 71028 и в соответствии с [1].
7.3 Требования электробезопасности к применяемому технологическому оборудованию и оснастке — по ГОСТ 12.1.019 и в соответствии с [2], правила безопасности при эксплуатации электроустановок — по [3].
7.4 Технологическое оборудование должно быть заземлено. Сечение заземляющих проводников — не менее сечения подводящих проводников; электрическое сопротивление между шиной заземления и узлами технологического оборудования, которые могут оказаться под напряжением, - не более 0,1 Ом по ГОСТ 12.1.019 и в соответствии с [2].
7.5 Требования пожарной безопасности — по ГОСТ 12.1.004, правила противопожарного режима в производственном помещении — в соответствии с [4].
7.6 Требования безопасности при эксплуатации сосудов, работающих под давлением, — в соответствии с [5].
7.7 Уровни шума и нормы вибрации на рабочем месте не должны превышать предельно допустимых значений поГОСТ 12.1.003 и ГОСТ 12.1.012 соответственно.
7.8 Содержание вредных химических веществ в воздухе рабочей зоны не должно превышать предельно допустимых концентраций по ГОСТ 12.1.007. Допустимые показатели микроклимата в рабочей зоне — поГОСТ 12.1.005.
12
ГОСТ Р 71837—2024
7.9 Работники, задействованные в ТП ЛР, должны быть обеспечены специализированными защитными очками для каждого типа лазерного излучения, специальной одеждой, обувью и средствами индивидуальной защиты в соответствии с требованиями нормативных документов.
7.10 Подъем и перемещение тяжестей (изделий массой более 16 кг) следует выполнять с применением подъемных механизмов.
7.11 Поверхности ограждений и перемещающихся узлов технологического оборудования должны быть окрашены в сигнальные цвета по ГОСТ 12.4.026. Для указания места нахождения огнетушителя или направления движения к этому месту следует использовать соответственно основной знак F04 или комбинированный знак пожарной безопасности по ГОСТ 12.4.026. На дверях помещений и лазерном технологическом оборудовании, на излучателе и в зоне обработки должны быть нанесены предупреждающие знаки W10 по ГОСТ 12.4.026 или предупреждающие знаки по ГОСТ IEC 60825-1; на электрооборудовании, дверцах силовых щитков, электротехнических шкафах — предупреждающие знаки W08 по ГОСТ 12.4.026.
13
ГОСТ Р 71837—2024
Приложение А (рекомендуемое)
Оптимальные параметры и режимы технологического процесса лазерной резки
А.1 Общие положения
А.1.1 Значение энергии лазерного излучения Е вычисляют по формуле
Е ^[Рс^пл + ^ПЛ + РС( ^И ^пл) + У’
(А.1)
где Q = /т ■ S — | ■ объем зоны нагрева, м3; |
Р — | ■ плотность материала, кг/м3; |
с — | ■ удельная теплоемкость материала, Дж/(кг • К); |
^и -^пл ^ПЛ | ■ температура испарения (кипения) материала, К; ■ точка плавления, К; ■ скрытая теплота плавления, Дж/кг; ■ скрытая теплота испарения, Дж/кг. |
А.1.2 Нормальную компоненту Vn скорости движения поверхности реза при плавлении материала вычисляют по формуле
V = * п L'
(А.2)
где Q — плотность мощности падающего излучения, поглощаемого элементом поверхности;
L — энергия разрушения единицы объема (эта энергия приравнивается к энергии, необходимой для того, чтобы материал нагреть от комнатной температуры То до температуры плавления Тт и расплавить), вычисляемая по формуле
L = cs₽s (Ъп _^о) + Рт^т> ^д 3)
где р® , Cj — плотность, кг/м3, и удельная теплоемкость металла, Дж/(кг • К), при начальной температуре То; рт — плотность при температуре плавления Тт, кг/м3;
Нт — удельная теплота плавления, Дж/кг.
Указанные представления справедливы при идеальном удалении жидкой фазы газовым потоком, когда толщина оставшейся пленки жидкости пренебрежимо мала.
А.1.3 Выбор длины волны оптимален для спектральной области, в которой металл или сплав имеет наибольший коэффициент поглощения. Частота и длительность следования импульсов должна определяться задачами обработки материала и требованиями к качеству реза. При резке небольших контуров или при резке в режиме ступенчатой мощности рекомендуется небольшая частота следования импульсов.
А.1.4 Следует учитывать, что при совпадении плоскости поляризации луча с плоскостью резки показатели скорости и качества резки повышаются. В этом случае на передней поверхности реза происходит наиболее высокое поглощение излучения. Если плоскость поляризации перпендикулярна к плоскости реза, то происходит поглощение излучения боковыми поверхностями реза. Скорость и качество резки могут значительно различаться в зависимости от изменения направления перемещения оптического устройства при вырезке фигурных заготовок. Для обеспечения наибольшей эффективности резки целесообразно плоскость поляризации пучка с помощью специального устройства автоматически поворачивать при изменении направления резки, чтобы она совпадала с плоскостью резки. Возможно превращение линейно поляризованного излучения в излучение с круговой поляризацией с применением фазовращающего зеркала, которое устанавливают перед входом в оптическое устройство. При использовании волоконных лазеров, в силу их конструктивных особенностей, эта рекомендация не актуальна.
А.1.5 Скорость резки следует выбирать в зависимости от вида металла (сплава) и толщины материала. Чем толще материал и чем выше температура плавления материала, тем дольше лазерный пучок должен воздействовать на место будущего реза. Завышенная или заниженная от оптимального значения скорость резки может привести к повышенной шероховатости, образованию грата, проплавлениям. Скорость резки также зависит от мощности лазера. Увеличение мощности способствует увеличению скорости резки.
А.1.6 Следует учитывать, что большое значение имеет качество применяемого газа. Давление газа следует выбирать в зависимости от толщины и вида материала.
А.1.7 Результат резки зависит от положения фокуса лазерного пучка. Его положение определяется толщиной разрезаемой детали (см. рисунок А.1): чем выше толщина, тем выше располагается фокус пучка. При резке с 14
ГОСТ Р 71837—2024
применением высокого давления положение фокуса перемещается в материал. Положение фокуса может определяться методом контура плазмы (изменения цвета плазмы) или определением минимальной толщины образуемой прорези на материале.
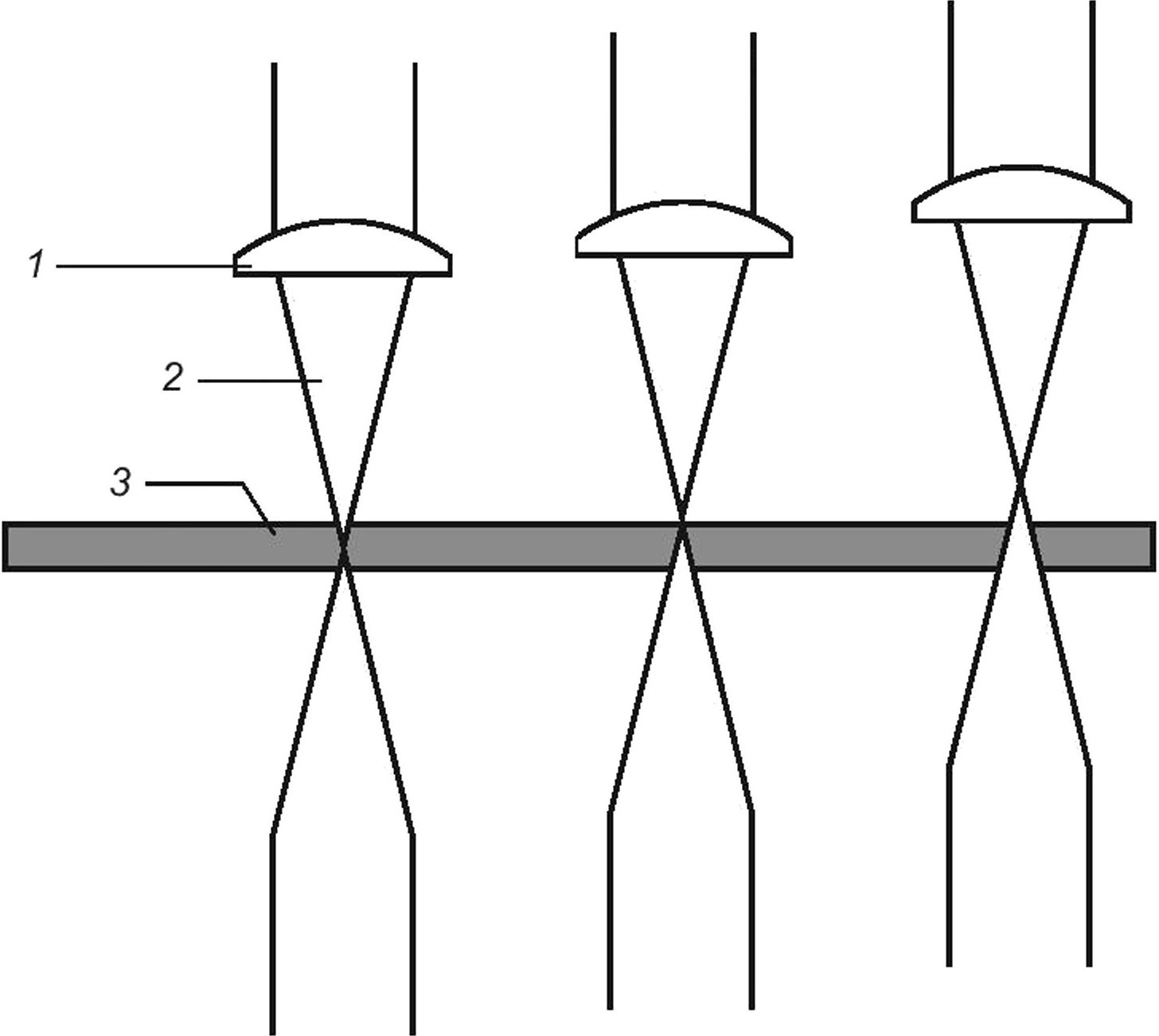
7 — линза; 2 — лазерный пучок; 3 — лист материала
Рисунок А.1 — Положение фокуса лазерного пучка: внутри, на поверхности и над поверхностью материала
А.1.8 Режимы и качество ЛР зависят от толщины материала. Чем толще материал, тем меньше скорость резки и тем больше шероховатость кромки реза при одном и том же типе лазера и его мощности. Параметры ТП ЛР будут определяться свойствами обрабатываемых материалов (коэффициентом поглощения, теплопроводностью, отражательной способностью, изначальной полировкой поверхности, содержанием примесей, легирующих элементов и пр.) При резке металлов с высоким содержанием углерода необходимо учитывать увеличение твердости материала вдоль кромки реза. При поддуве кислородом скорость ЛР увеличивается, но приводит к образованию большего количества окислов.
А.1.9 Шероховатые и матовые поверхности обеспечивают более высокую скорость резки. С учетом многообразия материалов (различные марки, способы производства, химический состав) и значительного различия в их свойствах следует учесть, что ЛР определяется использованием порядка 20 параметров, изменение которых может дать качественный рез.
А.1.10 На качество резки существенно влияет геометрия вырезаемых заготовок. Так, наличие острых углов, перемычек, небольших отверстий (диаметр меньше удвоенной толщины материала) вызывают сложности при резке. Обработку этих элементов следует проводить с уменьшенной скоростью резания, уменьшенной мощностью излучения, низкой частотой следования импульсов. При этом длительность импульса определяет тепловое и деформационное влияние на обрабатываемый материал. При коротком импульсе воздействия и большой плотности энергии определенный объем металла испарится и расплавится достаточно быстро, и тепло из зоны облучения не успеет распространиться по соседним зонам. Также длительность импульса определяет уровень механических воздействий вблизи зоны теплового воздействия и значение давления отдачи паров, которое обратно пропорционально т1/2, где т — длительность лазерного импульса. Размер зоны термического влияния, образующихся при воздействии лазерного излучения, пропорциональна т. Применение лазеров с более короткой длительностью импульса способствует получению лучшего результата обработки.
Эффективное время воздействия лазерного пучка т (без учета энергетических параметров) вычисляют по формуле
скан
где d0 — фокальный размер лазерного пучка;
^скан — скорость его сканирования по обрабатываемой поверхности.
Чем меньше диаметр сфокусированного лазерного пучка и скорость его сканирования, тем качество обработки будет выше.
15
ГОСТ Р 71837—2024
Библиография
[1] СанПиН 1.2.3685-21 Гигиенические нормативы и требования к обеспечению безопасности и (или) безвредности для человека факторов среды обитания
[2] «Правила технической эксплуатации электроустановок потребителей электрической энергии» (утверждены приказом Минэнерго России от 12 августа 2022 г. № 811)
[3] Правила по охране труда при эксплуатации электроустановок. ПОТЭУ (утверждены приказом Минтруда России от 15 декабря 2020 г. № 903н)
[4] Правила противопожарного режима в Российской Федерации (утверждены постановлением Правительства Российской Федерации от 16 сентября 2020 г. № 1479)
[5] Технический регламент О безопасности оборудования, работающего под избыточным давлением Таможенного союза
ТР ТС 032/2013
УДК 544.032.65:621.373.826:006.354
ОКС 25.220.99
Ключевые слова: оптика и фотоника, лазерная резка тонколистовых металлов и сплавов, технологический процесс
Редактор Н.В. Таланова
Технический редактор И.Е. Черепкова
Корректор О.В. Лазарева
Компьютерная верстка И.Ю. Литовкиной
Сдано в набор 06.12.2024. Подписано в печать 13.12.2024. Формат 60x84%. Гарнитура Ариал.
Усл. печ. л. 2,32. Уч-изд. л. 1,90.
Подготовлено на основе электронной версии, предоставленной разработчиком стандарта
Создано в единичном исполнении в ФГБУ «Институт стандартизации» , 117418 Москва, Нахимовский пр-т, д. 31, к. 2.